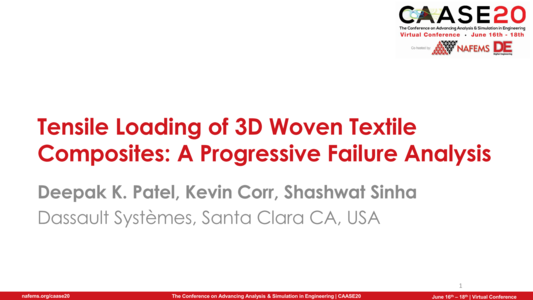
NAFEMS Americas and Digital Engineering (DE) teamed up (once again) to present CAASE, the (now Virtual) Conference on Advancing Analysis & Simulation in Engineering, on June 16-18, 2020!
CAASE20 brought together the leading visionaries, developers, and practitioners of CAE-related technologies in an open forum, unlike any other, to share experiences, discuss relevant trends, discover common themes, and explore future issues, including:
-What is the future for engineering analysis and simulation?
-Where will it lead us in the next decade?
-How can designers and engineers realize its full potential?
What are the business, technological, and human enablers that will take past successful developments to new levels in the next ten years?
Resource AbstractThe tensile response of hybrid 3D woven textile composites (3DWTCs) that consist of Glass, Carbon and Kevlar fiber tows, is simulated using a finite element (FE) based macroscale model. The fiber tows are embedded in an epoxy material and integrally woven into a single preform. Based on micromechanics concepts, homogenized property of the fiber tow is extracted from its fiber-matrix constituents numerically. The extracted properties are assigned to individual fiber tows, modeled discretely for different material systems. The enhanced mechanical properties of the textile composites are highly dependent on such hybrid configuration of multi-material systems and the orientations of fiber tows. 3DWTC is manufactured by laying up the warp and weft fiber layers and consequently running a Z-fiber in the thickness direction to bind the in-plane layers together. These composite structures offer a great advantage in terms of high resistance to layer delamination, which is a common problem in conventional laminated composites. They have high damage tolerance, high impact resistance and low fabrication cost, which makes them suitable for tailoring structural properties. Given these crucial benefits, these woven textile composites find widespread application in aerospace, automobile and defense industries. For simulation of these composite structures, it is necessary to accurately describe the mechanical properties of components to correctly predict their structural response under a given loading scenario. In this work, a representative volume element (RVE) unit is modeled with geometry and architecture inputs drawn from the literature. The simulation workflow is established with meshing the RVE, material modeling, and appropriate analysis procedure. To capture the progressive damage evolution in fiber tows, user defined material subroutine based on 3D Hashin’s damage law is developed. The RVE and the material models together provide a unique computational framework to predict the tensile strength of 3DWTCs, and its dependence on various geometrical and material parameters. The numerical simulation result predicts the global stress-strain response and the detailed local complex failure mechanisms of the textile composites. The reported results are found to be in good agreement with experimental data available in literature.