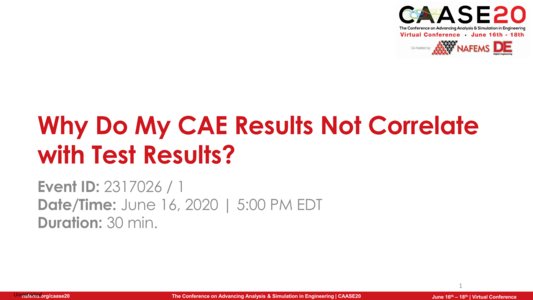
NAFEMS Americas and Digital Engineering (DE) teamed up (once again) to present CAASE, the (now Virtual) Conference on Advancing Analysis & Simulation in Engineering, on June 16-18, 2020!
CAASE20 brought together the leading visionaries, developers, and practitioners of CAE-related technologies in an open forum, unlike any other, to share experiences, discuss relevant trends, discover common themes, and explore future issues, including:
-What is the future for engineering analysis and simulation?
-Where will it lead us in the next decade?
-How can designers and engineers realize its full potential?
What are the business, technological, and human enablers that will take past successful developments to new levels in the next ten years?
Resource AbstractThis is an often perplexing issue for most CAE engineers in their career – why did my CAE result not match the test results? There must be something wrong with my model. While that is a possibility, in my career in CAE, the problem has often been attributed to testing conditions and more probable the “as manufactured” part did not represent the CAD model used for CAE.
The CAD model that CAE simulations are based on represent the ideal design with no tolerance variations, homogeneous material property distribution, no defects or porosity or cracks – yes it is perfect. Unfortunately, real parts are less than ideal. Often changes are introduced just before release of a design to address manufacturing and assembly issues. Typically, they are considered minor and should have negligible effect on performance – well that is what is hoped.
There are numerous examples where slight design deviations can result in substantial performance variation. In one instance, modification of a design radius a few millimeters to allow better casting flow at the foundry resulted in a product not meeting NVH requirements as simulated. When the part was laser scanned and the deviation identified, a new CAE simulation run on the reverse engineered laser scan point cloud identified that the design would not meet the NVH target.
In another example, despite frame structure parts not meeting dimensional quality targets, parts were tested and failed. Follow up reverse engineering and CAE simulation indicated the part would not achieve performance objectives. The problem in these instances was not having the “as manufactured” geometry for simulation. Unfortunately, engineering departments cannot be assured the parts being tested will meet the design requirements that were originally simulated.
But, the ability to quickly laser scan and reverse engineer these “as manufactured” parts and conduct CAE simulations is critical. This would significantly reduce the risk of running tests on parts that will fail. However, reverse engineering “as manufactured” parts can take a significant amount of time, and typically empirical test can be run faster.
Siemens PLM Software has developed a new methodology that automates the reverse engineering of laser scan point clouds and which can be used to generate a new CAE mesh or morph an existing mesh to match the laser scan data. In case studies, this has reduced reverse engineering and CAE time from 1-2 weeks to a couple of hours. Implementing such capabilities can free up CAE resources for other critical tasks, and more importantly quickly assess an “as manufactured” design to ensure it will meet requirements and performance objectives before validation tests.