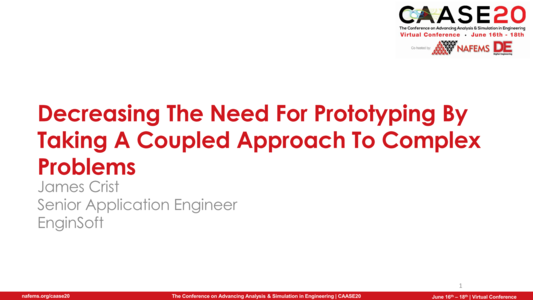
NAFEMS Americas and Digital Engineering (DE) teamed up (once again) to present CAASE, the (now Virtual) Conference on Advancing Analysis & Simulation in Engineering, on June 16-18, 2020!
CAASE20 brought together the leading visionaries, developers, and practitioners of CAE-related technologies in an open forum, unlike any other, to share experiences, discuss relevant trends, discover common themes, and explore future issues, including:
-What is the future for engineering analysis and simulation?
-Where will it lead us in the next decade?
-How can designers and engineers realize its full potential?
What are the business, technological, and human enablers that will take past successful developments to new levels in the next ten years?
Resource AbstractMany problems which are critical to simulation-driven design require multi-body dynamics and fluid dynamics knowledge, which until recently couldn’t be captured quickly enough using simulation to inform early design decisions. In the past these disciplines operated independently, sometimes because the problems were truly uncoupled, but also because the toolchain and computing hardware to perform these simulations weren‘t available. Advancements in commercial tools and available computer power at the desk and in the cloud make this problem approachable for use in today’s design environment. Implementing this approach early in the design lifecycle can return information to designers more quickly, reduce the need for prototyping, and ultimately allow for quicker time to market. This talk will present several examples of this approach across multiple industries.
Gearbox lubrication analysis is typically done with the prescribed motion of the gears, focusing only on the fluid behavior. This assumption can be valid, but in some cases the churning losses within the gearbox will be high enough to break this assumption, a problem that may not be caught until expensive physical testing is done. By coupling the fluid and dynamics problems the assumption is reduced to an input torque rather than a set speed. This change allows designers and analysts to understand how oil fill levels will affect not only lubrication but more broadly the gearbox performance. Depending on design stage and specifications this can be used to specify a necessary input torque for a specified output speed or generate curves of output speed based on a known input torque.
Proper understanding of vehicle dynamics requires a known mass distribution for the vehicle; gathering mass properties of most components is easy while including the mass of fuel is nontrivial. As the vehicle moves the fuel will slosh around, changing the handling of the vehicle and all of this changes with fill level, that is to say this is an inherently coupled problem. By efficiently co-simulating the fluid dynamics of the fuel with the vehicle handling simulation it is possible to run through a series of handling tests while varying fuel tank placement, design, and fill level to approach an optimal design. This requires many iterations but much of the work can be automated in the initial model setup.
These examples demonstrate the need for coupled simulations of dynamics and fluids, and how this type of analysis can be implemented in today’s workflows.