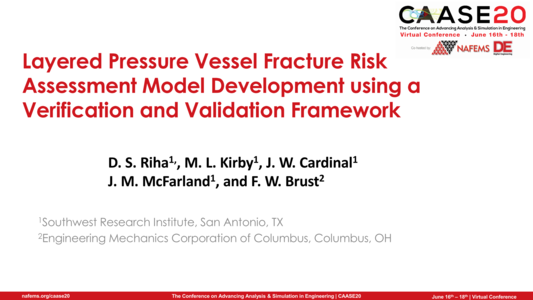
NAFEMS Americas and Digital Engineering (DE) teamed up (once again) to present CAASE, the (now Virtual) Conference on Advancing Analysis & Simulation in Engineering, on June 16-18, 2020!
CAASE20 brought together the leading visionaries, developers, and practitioners of CAE-related technologies in an open forum, unlike any other, to share experiences, discuss relevant trends, discover common themes, and explore future issues, including:
-What is the future for engineering analysis and simulation?
-Where will it lead us in the next decade?
-How can designers and engineers realize its full potential?
What are the business, technological, and human enablers that will take past successful developments to new levels in the next ten years?
Resource AbstractA large effort is underway by the National Aeronautics and Space Administration (NASA) to assess the fitness-for-service of a diverse fleet of nearly 300 aging metallic layered pressure vessels. The vessels in the fleet are located across multiple NASA centers and range from 3-layer to 32-layer vessels. This effort involves a multi-disciplinary team of engineers performing structural analysis and modeling, materials testing, and non-destructive evaluation. The objective of this effort is to understand the relative risk of failure of a vessel due to manufacturing defects and fatigue crack growth of sub-critical flaws as a result of cyclic service loading (pressurization and depressurization of the vessels during service). For many of the vessels in the fleet, a traditional fitness-for-service evaluation is overly conservative because of uncertainties in the material properties, geometry, and stress-state in the vessels. Therefore, uncertainty and variability in the vessels are being quantified and mature models of the stress-state and fracture mechanics response at locations of interest in the vessels are being exercised in a probabilistic framework using the NESSUS® probabilistic analysis software. In the probabilistic framework, inputs to the models are treated as random variables and the models are linked together to predict the cumulative distribution function of the response, analyze the sensitivity of the response to the random variable inputs, and perform a reliability analysis.
The primary locations of interest for probabilistic risk assessments of the vessels in this study were the head-to-shell and shell-to-shell circumferential welds and the longitudinal welds. Variability in the predicted stress-state in these regions of the vessels has been shown to be dominated by uncertainty in the weld residual stress field, which was simulated by a sequentially coupled thermo-mechanical finite element model with variation ascribed to the temperature-dependent stress-strain curve and coefficient of thermal expansion of the materials in the model. Another finite element model was used to predict the service stress field due to the applied pressure, and then, via the principal of superposition, the resulting stress field (service stress + weld residual stress) was provided as an input to the NASGRO® fracture mechanics software to predict the fracture mechanics response at the locations of interest. The responses predicted in this study included, the stress intensity factor, critical crack size, critical initial flaw size, and number of cycles to failure for cyclic service loading, which were primarily sensitive to uncertainty in the fracture toughness (KJc) and weld residual stress field. Since some of the ferritic steels used in vessel fabrication could experience cleavage fracture at operating temperatures, this was also accounted for in the stochastic analysis by sampling a distribution of the lowest annual temperature based on the geographic location of the vessel. The probabilistic risk assessments, such as the probability that the stress intensity factor exceeds the fracture toughness of the material for a given crack size, and the predictions of critical crack size and critical initial flaw size are being used to guide non-destructive evaluation requirements and potential development efforts. This presentation will focus on uncertainty quantification and probabilistic methods used in this effort and will provide examples of stochastic analysis that was performed for demonstration vessels in the fleet using the probabilistic framework.