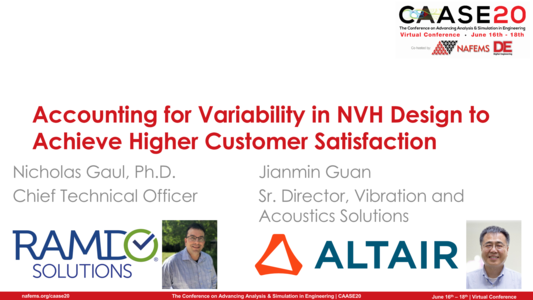
NAFEMS Americas and Digital Engineering (DE) teamed up (once again) to present CAASE, the (now Virtual) Conference on Advancing Analysis & Simulation in Engineering, on June 16-18, 2020!
CAASE20 brought together the leading visionaries, developers, and practitioners of CAE-related technologies in an open forum, unlike any other, to share experiences, discuss relevant trends, discover common themes, and explore future issues, including:
-What is the future for engineering analysis and simulation?
-Where will it lead us in the next decade?
-How can designers and engineers realize its full potential?
What are the business, technological, and human enablers that will take past successful developments to new levels in the next ten years?
Resource AbstractThe automotive industry is extremely competitive with customer satisfaction being one of the driving factors. Customers expect their vehicles to be of the highest quality, meaning fuel efficient, high durability, and a smooth and quiet ride. Automotive NVH engineers are constantly working on trying to meet this high customer satisfaction by improving vehicle designs to provide the quietest vehicle possible. The traditional NVH approach is to use deterministic optimization together with NVH simulations in order to find a vehicle design that has a noise level under a given threshold. When the industry first started to do this, it was a great technic in order to lower vehicle noise levels significantly and increase customer satisfaction. In order to maintain a competitive edge by achieving higher customer satisfaction with the ever-increasing customer expectations, the automotive industry is constantly seeking new technics to help them further improve the NVH performance of their vehicles. Now that deterministic optimization is becoming more of a standard practice in the automotive industry for improving NVH performance, the next step to try to further improve NVH performance is to account for the variability in manufacturing and material properties. With NVH simulations constantly improving and computing capabilities continuously growing, studying the affect of manufacturing and material property variability is a much more feasible problem. NVH problems are extremely challenging with a large number of variables and the noise response being a nonlinear function in terms of the variables. Uncertainty quantification (UQ) can be used to account for the manufacturing and material property variability, referred to as the input variability, in order to determine the variability in the noise level. The variability of the noise level is referred to as the output variability. In this work it will be shown how UQ is used together with NVH simulations to propagate the input variability, i.e., the manufacturing and material property variability, in order to obtain the noise level variability. The noise level variability will be captured as distributions. The distributions of the noise level are then used to plot NVH curves, i.e., noise vs. frequency, that show the variability in the noise level by plotting the 95% interval band of the NVH curve. These noise variability curves provide a powerful and simple way of understanding the variability in the noise level. These curves let the engineer easily see how much variability can be expected in the noise level for a given design at each frequency. The new standard for NVH is to account for the noise level variability and have it under some target noise level threshold. It will be shown how reliability-based design optimization (RBDO) can be used to achieve exactly this. The engineer defines a noise level threshold and target reliability, in the example shown the noise level threshold is 57 dBA and the target reliability defined to be 90%. This means that when considering the noise level variability, 90% of the noise level will be less than the 57 dBA threshold. It will be shown that by carrying out RBDO it is possible to find a design that achieves these targets. Thus, by using UQ and RBDO the NVH engineer can achieve an even higher level of NVH performance, thus, further improving customer satisfaction.