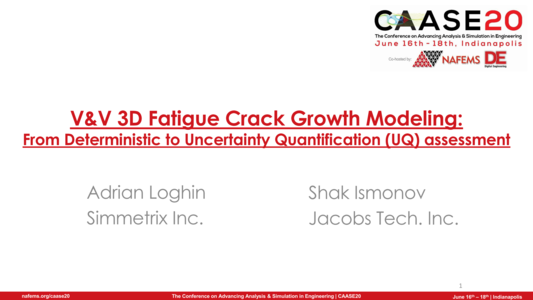
NAFEMS Americas and Digital Engineering (DE) teamed up (once again) to present CAASE, the (now Virtual) Conference on Advancing Analysis & Simulation in Engineering, on June 16-18, 2020!
CAASE20 brought together the leading visionaries, developers, and practitioners of CAE-related technologies in an open forum, unlike any other, to share experiences, discuss relevant trends, discover common themes, and explore future issues, including:
-What is the future for engineering analysis and simulation?
-Where will it lead us in the next decade?
-How can designers and engineers realize its full potential?
What are the business, technological, and human enablers that will take past successful developments to new levels in the next ten years?
Resource AbstractValidation & Verification (V&V) is a continuous effort in modeling development. As engineering software improves, cheaper computational resources become available and, technology provides higher resolution physical measurements, the V&V process needs to leverage novel capabilities to bring knowledge and benefits to the engineering design community. Different organizations (ASME, TMS) have issued documents recognizing the importance of V&V in engineering design and laying out
guidelines for achieving and maintaining the V&V goals [1, 2]. An integral part of these V&V guidelines is Uncertainty Quantification (UQ), a tool designed to provide a relationship between model predictions and uncertainties related to experimental data or, uncertainties related to the model itself [3, 4].
Three-dimensional (3D) fatigue crack growth modeling is used as a case study for an uncertainty quantification V&V assessment. Different experimental measurements and 2D numerical assessments from the literature are considered as a reference for V&V purposes. 3D finite element models (FEM) representative of the specimen geometry and test procedure are used for deterministic fatigue crack growth assessment [5]. The procedure to perform crack propagation simulation is automatic and robust which allows a large number of simulations to be performed quickly. This capability is used along with the Latin Hypercube Sampling (LHS) technique to establish a predefined set of model configurations, perform independent 3D crack propagation simulations and predict crack path for each configuration. Typical parameters used in this design of experiment setup are (but not restricted to): initial crack size, crack location, and the position of geometric features. Once all simulations are available, a Radial Basis Function (RBF) response surface is used to train a model that can be efficiently used in probabilistic Monte Carlo (MC) simulations. In addition to the geometric parameters mentioned above, stochastic variability of the fatigue crack growth rate measurement is also considered in the study to evaluate remaining useful life (RUL) scatter. The probabilistic predictions are compared against experimental measurements to quantify the impact of uncertainty of different factors on the fatigue crack growth predictions.
V&V development coordinated with UQ assessment is a necessary step to quantify confidence bounds related to component level performance predictions such as fatigue crack growth life assessment presented here. Component level implementations of Structural Health Monitoring (SHM) or more recent Digital Twin (DT) concepts can benefit from recent development of explicit 3D FEM based crack propagation simulation capabilities and readily available machine learning (ML) algorithms to reach an accuracy-efficiency compromise in performing probabilistic life assessment.