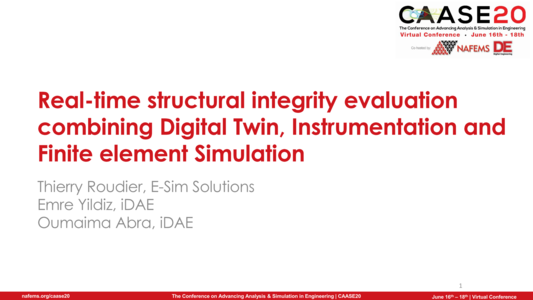
NAFEMS Americas and Digital Engineering (DE) teamed up (once again) to present CAASE, the (now Virtual) Conference on Advancing Analysis & Simulation in Engineering, on June 16-18, 2020!
CAASE20 brought together the leading visionaries, developers, and practitioners of CAE-related technologies in an open forum, unlike any other, to share experiences, discuss relevant trends, discover common themes, and explore future issues, including:
-What is the future for engineering analysis and simulation?
-Where will it lead us in the next decade?
-How can designers and engineers realize its full potential?
What are the business, technological, and human enablers that will take past successful developments to new levels in the next ten years?
Resource AbstractDigital twins and finite element calculations are frequently used to do predictive simulation of structural integrity and service life estimations. These simulations are based on estimated load cases that is assumed to represent the ultimate loads that the structure may be subject to.
However, the real load history that a structure is subjected to, may be very different than the estimations. In some cases, a critical part whose service life is estimated by duration in service may not be solicited as often as predicted. This is a case of unnecessary early replacement of a part. The contrary would result, however, in safety issues. If a part is more solicited by an aggressive use, the service life may be a lot shorter than the predicted one. In such cases, a real-time evaluation of structural integrity with a continuous feedback to the user may prevent damages, accidents and in some cases life losses.
This paper presents a technology demonstration where a digital twin is analysed real-time, using measured loads acting on a simple structure. The applied true loads are obtained using a limited number of sensors and the digital twin is continuously analyzed with recorded loads. The finite element analysis is used to compare the deformed shape to analysis results as a validation method. The stress history of the studied part is continuously fed to a simultaneous fatigue analysis where the load cycle counting using rainflow technique is updated. The user is provided with a simplified interface with two important information: Ratio of applied load to load capacity and estimated remaining service life.
The approach is also innovative thanks to powerful co-simulation platforms allowing native interoperability between simulated components and real-time instrumentation. Using co-simulation through a collaborative solution provides a generic approach enabling the engineering teams to setup their own simulation environment, using different types of solvers and simulation engines. Such a platform makes easier the integration of models with different levels of maturity/complexity and promotes better integration with MBSE methodology.