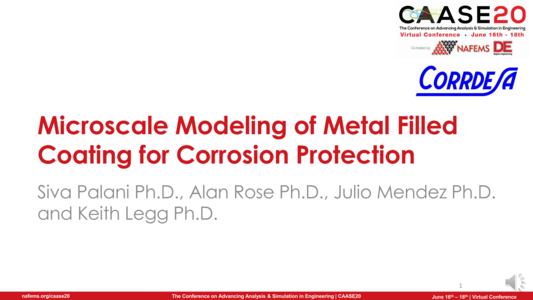
NAFEMS Americas and Digital Engineering (DE) teamed up (once again) to present CAASE, the (now Virtual) Conference on Advancing Analysis & Simulation in Engineering, on June 16-18, 2020!
CAASE20 brought together the leading visionaries, developers, and practitioners of CAE-related technologies in an open forum, unlike any other, to share experiences, discuss relevant trends, discover common themes, and explore future issues, including:
-What is the future for engineering analysis and simulation?
-Where will it lead us in the next decade?
-How can designers and engineers realize its full potential?
What are the business, technological, and human enablers that will take past successful developments to new levels in the next ten years?
Resource AbstractCoatings are generally classified in accordance with the mechanisms by which they protect a metal against corrosion, namely barrier protection, passivation/ inhibition and sacrificial protection. Metal filled coatings/primers containing anodic materials for example are engineered to provide sacrificial protection to the underlying metal. These coatings rely on the principle of galvanic corrosion for the protection of metals against corrosion. This means that the substrate is protected by a pigment alloy that is electrochemically more active than the material to be protected. In recent years, metal filled coatings have been gaining an increasing share of the aerospace and defense market, in a large part because environmental restrictions both in the US and particularly in Europe are driving the aerospace and defense industry away from the use of legacy hexavalent chromium (Cr6+) containing primers which are found to be very toxic. One of the few viable primers without Cr6+ is metal filled primer containing anodic materials.
In particular, the aluminum rich (Al-Rich) primer developed by Naval Air Systems Command (NAVAIR) has shown some very promising results and important advantages that it provides electrochemical protection to aluminum, steel, and other metallic objects to withstand the severe corrosive operating environments.
However, development and optimization of these coating systems is inhibited by a lack of understanding of how the entire system behaves and protects coated components, and assemblies in which they are used. Furthermore, the technology to manufacture these primers is quite advanced with regards to particulate size, loading and a number of other parameters that can be manipulated.
To support this process, we have developed a novel computational CAE model employing Discrete element method (DEM) and Computational fluid dynamics (CFD) to create a 3-D model of the metal-filled primer, incorporating both its physical microstructure and its electrochemical properties that can be used to determine how it will interact electrochemically with the substrate and adjacent materials. Consequently, these models are aimed to help to identify and understand the key parameters for coating development, such as particle loading, particle size, shape and treatments, resin/media properties, etc. on the corrosion protection performance.
This paper will present corrosion models of Al-rich primer applied on an aluminum substrate. Using case studies, we will demonstrate how it is now possible to illustrate sacrificial anode based cathodic protection mechanism capabilities of the anodic particle spatially in a 3-D primer microstructure in terms of electric potential and current density distribution, and providing some insight on the depletion of the pigment particles as a function of their electrochemical properties, primer electrolyte conductivities, and their location within the primer layer.