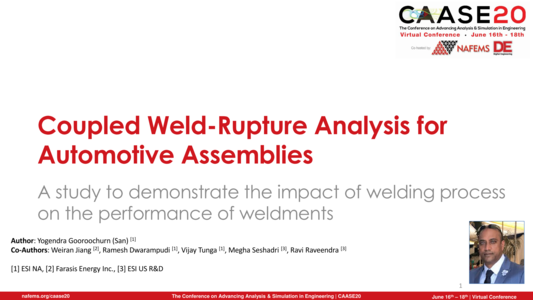
NAFEMS Americas and Digital Engineering (DE) teamed up (once again) to present CAASE, the (now Virtual) Conference on Advancing Analysis & Simulation in Engineering, on June 16-18, 2020!
CAASE20 brought together the leading visionaries, developers, and practitioners of CAE-related technologies in an open forum, unlike any other, to share experiences, discuss relevant trends, discover common themes, and explore future issues, including:
-What is the future for engineering analysis and simulation?
-Where will it lead us in the next decade?
-How can designers and engineers realize its full potential?
What are the business, technological, and human enablers that will take past successful developments to new levels in the next ten years?
Resource AbstractThe development for lightweight-driven design of vehicles in automotive industry necessitates the use innovative materials such as steel (high strength steel (HSS), ultra-high strength (UHSS), advance high strength steel (AHSS) and Aluminum alloys) and aluminum (series 5000 and 6000) alloys to meet performance requirements. Suppliers usually achieve performance requirement such as strength by altering the chemical composition of these alloys. Different strengthening mechanisms such as work hardening, and heat treatment are typically used to meet the initial strength requirements. When these alloyed structures are welded together, depending on the welding heat input, the material chemistry and thickness, they either harden or soften in the heat affected zone, which in turn affects the performance of the weldment during service.
Traditionally, performance analyses such as crash, rupture, fatigue, etc. of weldments using computational methods like finite element methods use base material properties that do not consider change of microstructure and mechanical properties in the heat affected and fusion zones due to welding. Given the fact that welding processes affect the mechanical properties in the heat affected zone, using base material properties to represent the areas surrounding the weld during finite element analyses can either over or under predict the performance which in turn hinder/limit potential weight reduction strategies. Computational weld analyses can accurately predict the changes in the microstructures and mechanical properties in the heart affected zone in addition to the prediction of deformation, residual stresses and plastic strains. Thus, accurate prediction of performance of structures made of these welded alloys requires the incorporation of the welding effects through the coupling of welding simulation with performance simulation. In this presentation, examples problems are used to demonstrate the impact of welding processes on the performance of weldments by coupling ESI’s welding software SYSWELD with the performance software VPS, seamlessly. A final example that demonstrates the applicability of the coupled weld-rupture analysis to the solution of an industrial problem will be presented by investigating an automotive battery package.