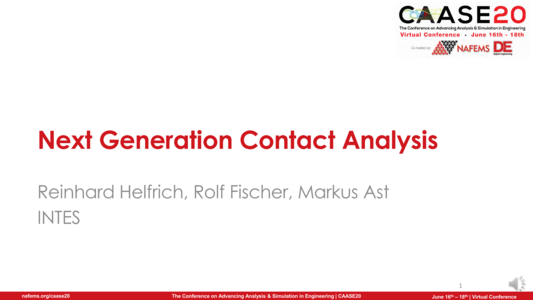
NAFEMS Americas and Digital Engineering (DE) teamed up (once again) to present CAASE, the (now Virtual) Conference on Advancing Analysis & Simulation in Engineering, on June 16-18, 2020!
CAASE20 brought together the leading visionaries, developers, and practitioners of CAE-related technologies in an open forum, unlike any other, to share experiences, discuss relevant trends, discover common themes, and explore future issues, including:
-What is the future for engineering analysis and simulation?
-Where will it lead us in the next decade?
-How can designers and engineers realize its full potential?
What are the business, technological, and human enablers that will take past successful developments to new levels in the next ten years?
Resource AbstractContact is a highly nonlinear boundary condition in Finite Element Analysis (FEA), which is used in many applications. Each assembly model has joints where contact is present. An accurate representation of the actual contact has a great influence on displacements and stresses. In fact, even very small changes in the contact geometry can change the FE results drastically.
Although contact is omnipresent in FEA applications, the standing of contact analysis is still rather poor due to high computational effort as well as sometimes serious convergence and accuracy problems. Such problems can also limit the possible model sizes due to increasing computing times. Users often replace true contact by other couplings and hope that the results will be acceptable. When model sizes increase due to needs for predicting durability, the situation becomes even worse. Additional computational effort will be needed, if contact is taken into account together with elastic-plastic material behavior and geometrical nonlinearities.
Therefore, a contact solver is needed, which provide accurate results and very short computation times. The accuracy is achieved by two points: (1) Lagrangian multipliers are used to properly describe the contact conditions correctly, which do not allow for tensional contact forces, show no penetration of the contact surfaces, and provide contact forces only for closed gaps. (2) A flexibility approach is used as constitutive equation, because contact forces are the primary unknowns in contact analysis. The performance aspect is supported by a condensation approach, which reduces the problem size dramatically and allows for a very efficient solution based on state-of-the art solution strategies.
This paper introduces a new solver for contact analysis, which opens a door to very large models (> 150 Million DOF) with contacts (> 200,000) and accomplishes top speed (overnight) without sacrificing accuracy. Various industrial examples are shown to illustrate the achievements in different application areas.