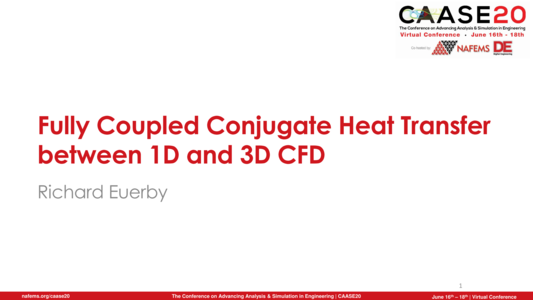
NAFEMS Americas and Digital Engineering (DE) teamed up (once again) to present CAASE, the (now Virtual) Conference on Advancing Analysis & Simulation in Engineering, on June 16-18, 2020!
CAASE20 brought together the leading visionaries, developers, and practitioners of CAE-related technologies in an open forum, unlike any other, to share experiences, discuss relevant trends, discover common themes, and explore future issues, including:
-What is the future for engineering analysis and simulation?
-Where will it lead us in the next decade?
-How can designers and engineers realize its full potential?
What are the business, technological, and human enablers that will take past successful developments to new levels in the next ten years?
Resource Abstract1D and 3D CFD co-simulation has always been a hot topic in the simulation community, leveraging the speed and flexibility of 1D and the fidelity of 3D in a single solution is very appealing for engineering applications. The complexity of models in recent years has increased dramatically and different methods for simulating these complex problems have been created with co-simulation being one of these. Classic co-simulation approaches transfer boundary condition information at predefined time steps during a solution process. However, this approach has stability and accuracy limitations.
Simcenter Flomaster and Simcenter FLOEFD have demonstrated that fully implicit coupling, using the “OneSim” aggregated temperature and pressure solver, is more stable and accurate. This allows fluids from the 1D domain to flow in and out of the 3D domain and is applicable to both steady and transient solutions.
This capability has now been extended to allow linear elements in the system model to exchange heat directly along their length with the 3D domain. For conjugate heat transfer, a ‘chain’ of 1D components is associated with 2D CAD faces, through which heat is exchanged. The conjugate heat transfer is simulated using the same implicit, aggregated solver approach as the hydraulic coupling.
This technology has applications far beyond simple geometries and pipes in a 3D domain. It can be used in large heat exchangers applications where the pipe work is too complex to be resolved using 3D CFD within a reasonable time frame. It can be used to assess the performance and reliability of heat transfer in complex 3D systems, e.g. in Gas Turbines – 3D primary flow over a 3D solid blade with 1D internal duct and secondary air system model.
This paper will provide a case study showing the use of this technology in various heat exchangers and how this novel technology increases the simulation speed whilst also retaining the accuracy in the simulation.