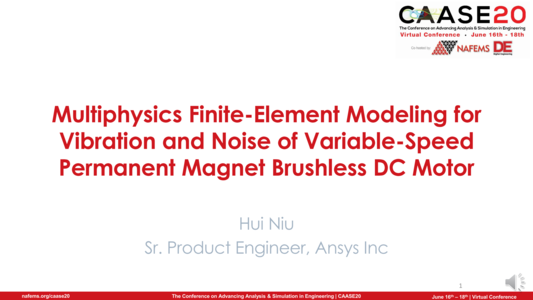
NAFEMS Americas and Digital Engineering (DE) teamed up (once again) to present CAASE, the (now Virtual) Conference on Advancing Analysis & Simulation in Engineering, on June 16-18, 2020!
CAASE20 brought together the leading visionaries, developers, and practitioners of CAE-related technologies in an open forum, unlike any other, to share experiences, discuss relevant trends, discover common themes, and explore future issues, including:
-What is the future for engineering analysis and simulation?
-Where will it lead us in the next decade?
-How can designers and engineers realize its full potential?
What are the business, technological, and human enablers that will take past successful developments to new levels in the next ten years?
Resource AbstractThe global demand for greater power efficiency is driving electrification initiatives across industries. In automotive industry, new electric powertrain architectures have been widely developed. Complexity of electric powertrain and driveline introduces high frequency tonal noise from engine and transmission systems. Acceptable audible noise levels for transportation vehicles must meet legislation and customer satisfaction. Therefore, NVH impact is particularly significant in electric powertrain design.
This work derives multiphysics finite element modeling process to predict vibration and noise due to magnetic force of a permanent-magnet brushless DC motor. The motor in study is a three-phase surface-mount permanent-magnet brushless DC motor with 4 poles, and 24 slots. Magnetic force computation in two-dimensional electromagnetic model is carried out over a variable speed range magnetic transient analysis. Using discrete Fourier transformation and electromagnetic-structural one-way coupling schemes, magnetic harmonic forces for every rotation angular speed are generated and applied on stator teeth’s inner surfaces. In Mechanical pre-processing, a 3D finite element model of brushless DC motor, including housing, caps, bearings, and shaft beam, is built for comprehensive Multiphysics analysis. Vibration characteristics are calculated for the three-dimensional full finite element model of the motor in multiple-RPM (MRPM) mode-superposition (MSUP) harmonic response analysis. Waterfall diagram of equivalent radiation pressure level (ERPL) contour plotting in function of rotation angular speed and frequency is obtained in multiple RPM harmonic analysis. Further, surface vibrating velocities for every rotation angular speed are imported and applied on acoustic domain using fluid-structure interaction one-way coupling. Noise radiated from motor housing including front and end caps is evaluated. In MRPM harmonic acoustic analysis, far-field sound pressure level (SPL) waterfall diagram in function of rotation angular speed and frequencies is obtained. Waterfall data of far-field SPL is adopted to perform the sound quality analysis based on magnetic force excited acoustic noise. Finally, the comprehensive psychoacoustic analysis including loudness, loudness level and sharpness variation over time, and their maximum, is performed.