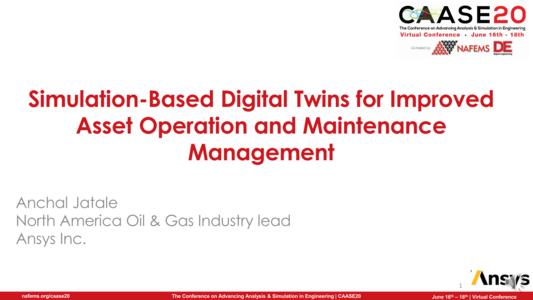
NAFEMS Americas and Digital Engineering (DE) teamed up (once again) to present CAASE, the (now Virtual) Conference on Advancing Analysis & Simulation in Engineering, on June 16-18, 2020!
CAASE20 brought together the leading visionaries, developers, and practitioners of CAE-related technologies in an open forum, unlike any other, to share experiences, discuss relevant trends, discover common themes, and explore future issues, including:
-What is the future for engineering analysis and simulation?
-Where will it lead us in the next decade?
-How can designers and engineers realize its full potential?
What are the business, technological, and human enablers that will take past successful developments to new levels in the next ten years?
Resource AbstractThe insight of physics-based simulation in conjunction with advancement in collection and usage of sensor data enabled by the wireless technology and cloud computing has created great opportunities. It can drastically reduce risks associated with cost and schedule overruns resulted in less warranty cost and unexpected downtime. Simulation technology plays a central role in increasing the ROI related to IoT and digital-twin initiatives. It can provide insight from the deployment stage of the IoT platform to its operation and end of life. This includes sensor placement optimization to physics-based data interpretations and physics-based decision making. Additionally, it is being used for monitoring, diagnostics, prognostics, and prescriptive resolutions to optimize asset performance and utilization and record the digital footprint of the system. This technology also provides valuable insight for future product, system and subsystem requirements and design.
Current talk will present a solution for digitalization of assets/process using the power of detailed 3D simulations. The solution will be showcased with an industrial scale shell & tube heat exchanger. The failure modes like fouling, corrosion, fatigue was modeled using 3D physics simulation models (CFD and FEA). Traditionally these models take long time to execute making them not suitable for real-time monitoring. Thus, the details of 3D models were compressed in a lightweight real-time model (Reduced order modeling) which were then hosted on an IOT platform and connected to the sensor data. This 3D detailed simulation powered twin provides insights into the equipment which was not possible with just the data. This twins augment and extend the capability to understand how and why certain failure is happening, enabling the person on the field to take informed decisions. This portable digital twins (run-times) can also be used as virtual sensors or to determine the physical sensor placement.