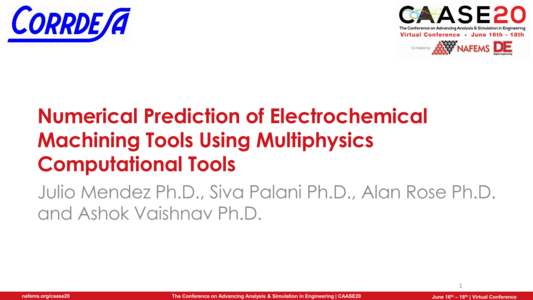
NAFEMS Americas and Digital Engineering (DE) teamed up (once again) to present CAASE, the (now Virtual) Conference on Advancing Analysis & Simulation in Engineering, on June 16-18, 2020!
CAASE20 brought together the leading visionaries, developers, and practitioners of CAE-related technologies in an open forum, unlike any other, to share experiences, discuss relevant trends, discover common themes, and explore future issues, including:
-What is the future for engineering analysis and simulation?
-Where will it lead us in the next decade?
-How can designers and engineers realize its full potential?
What are the business, technological, and human enablers that will take past successful developments to new levels in the next ten years?
Resource AbstractComputational Fluid Dynamics (CFD) and Finite Element Analysis (FEA) have become the norm in engineering design and scientific applications, whereas other areas such as electrochemistry and their applications are still in their exploratory stage. Electrochemical Machining (ECM) essentially harnesses corrosion to machine very hard metals, since the tool never needs to touch the workpiece unlike conventional cutting and milling techniques. Presently, an Edisonian approach is typically used for designing ECM tools to account for the complex flow field found in the electrolyte flow region. Flow phenomena such as turbulence, hydrogen evolution and large gradients in temperature field combine with electrodynamics and Joule heating to make the flow highly inhomogeneous. As a result, ECM tools (cathode) go through several design iterations to achieve the desired shape on the workpiece (anode). So, although ECM is a very attractive machining process the effort and cost involved in tooling design deters its widespread use.
With the advent of High-Performance Computing (HPC), efficient numerical algorithms and multiphysics CFD packages ECM simulations are gaining popularity in the CFD community. Nevertheless, one of the main challenges is still unresolved “the large grid deformation required to represent the tool motion”. This work shows a novel technique where the ECM is modeled using an efficient re-meshing algorithm that allows large deformation without incurring low mesh metrics and/or numerical instabilities. This technique was tested using a primary current distribution methodology to solve the die-sinking configuration which numerical predictions agreed fairly well with the digital 3D optical profilometry data gained from ECM on test specimens. Preliminary results demonstrate this methodology is computationally more efficient than overset methods, although a certain deviation was found due to round off errors in the interpolation and reconstruction methods used in morphing techniques. This deviation was drastically reduced as the mesh was further refined in the areas where large deformation was present.