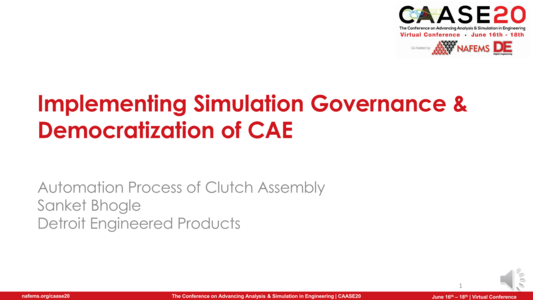
NAFEMS Americas and Digital Engineering (DE) teamed up (once again) to present CAASE, the (now Virtual) Conference on Advancing Analysis & Simulation in Engineering, on June 16-18, 2020!
CAASE20 brought together the leading visionaries, developers, and practitioners of CAE-related technologies in an open forum, unlike any other, to share experiences, discuss relevant trends, discover common themes, and explore future issues, including:
-What is the future for engineering analysis and simulation?
-Where will it lead us in the next decade?
-How can designers and engineers realize its full potential?
What are the business, technological, and human enablers that will take past successful developments to new levels in the next ten years?
Resource AbstractAutomation is very important part of industry 4.0 and it is no different in the virtual validation scenario as well. Traditionally CAE model building activities that are time consuming have been core focus of automation besides creating presentation files from the FE results data base. In most organizations CAE SoPs (standard operating procedures) are already in place. This satisfies one of the important necessary conditions for initiating automation. Today, as the product development cycle time is being shrunk there is more emphasis on virtual validation. This has led to more workload for CAE/FE analysts. Automation of the CAE SoP provides an opportunity to CAE/FE analysts to overcome the time crunch without any compromise to quality of results. In this paper, effort is being made to explain a novel approach to CAE process automation. The paper looks at automation for preparing ready to run FE model of clutch assembly. The Clutch assembly is usually built with some parts that are discretized with hexa elements and others with higher order tetra elements. This depends on the SoP or best practice followed by engineering teams. The process automation that is discussed in this paper is designed to generate ready to run solver deck from input CAD data. This process automation captures geometry clean-up tasks for clutch assembly parts, meshing clutch assembly parts as per the guidelines or SoP, assigning material properties, creating connection as per model assembly guidelines and creating the analysis load steps. Smart processes to automatically define contacts and auto fix contacts are being added to further save engineers’ time. The process automation does require inputs from the user and they are channeled through “drag and drop” menus or User Panels that are easy to create. These are a part of process automation methodology. The key four steps for the process automation are Record, Create UI, Plumb the Process and Publish. Auto parameterization of the FE model provides ability to add intelligence to the FE model assembly. This ability eases the ‘what if’ scenario. This holistic process is estimated to save time drastically upwards of 50 percent to the CAE user. The Process Automation that is created by a CAE engineer using the above mentioned process does not require an expertise with any programming language. CAE activities in product development tend to be resource intensive. CAE process automation is very important to reduce the time spent on mundane CAE activities including certain pre-processing and post-processing steps. This is the inception for democratizing CAE activities as it enhances the efficiency from all resources.