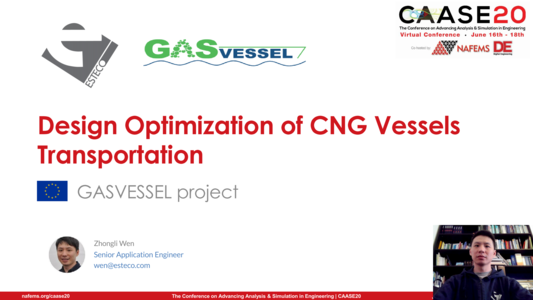
NAFEMS Americas and Digital Engineering (DE) teamed up (once again) to present CAASE, the (now Virtual) Conference on Advancing Analysis & Simulation in Engineering, on June 16-18, 2020!
CAASE20 brought together the leading visionaries, developers, and practitioners of CAE-related technologies in an open forum, unlike any other, to share experiences, discuss relevant trends, discover common themes, and explore future issues, including:
-What is the future for engineering analysis and simulation?
-Where will it lead us in the next decade?
-How can designers and engineers realize its full potential?
What are the business, technological, and human enablers that will take past successful developments to new levels in the next ten years?
Resource AbstractThis article reports the main achievements of the European project called ‘GASVESSEL’, which aim to open up new possibilities to exploit stranded, associated and flared gas where this is currently not economically feasible as well as to increase the gas transport possibilities of currently exploited gas fields with a new cost effective CNG (Compressed Natural Gas) transport concept. This can globally unlock up to at least € 35 billion/Yr worth of gas as such helping to rebalance the European and global energy security equations.
GASVESSEL will innovate different steps in the value chain; from a decision support model to simulate and benchmark costs of the novel CNG concept against alternative gas transporting systems until the ship design and manufacturing process of the innovative lightweight Composite Overwrapped Pressure Vessels (PV’s). The innovation of the CNG transport concept is enabled by a novel patented solution for the manufacturing of up to 70% lighter Pressure Vessels compared to steel alternatives, enabling new CNG ship designs with much higher payloads and therefore dramatically lower transportation cost per m3 of gas.
The optimization software modeFRONTIER and VOLTA web-based solution have been used by the partners in the different phases of the Project for the design of the system.
In function of each different geographical scenarios (which includes East Mediterranean, Barents Sea and Black Sea) and gas demand, parameters such as ship size and number, storage and facilities units at the ports have been optimized in order to reduce the transportation costs and therefore gas tariff.
Components of the gas vessels, material and type of the fibers that wraps the liner, have been then optimized to minimize weights while respecting high value of safety factors.
Using traditional pressure vessels the relevant thickness of the walls induces both a significant weight of the vessels and a limited ratio between the volume of the transported goods and the total one, comprehensive of the tanks themselves. To overcome these issues, it is possible to manufacture the tanks using an internal thin metal liner wrapped with several layers of fiber-reinforced composite materials (filament winding); the obtained structure, being light and stiff, assures that the transportation of the compressed natural gas can be competitive in the market.
The filament winding is a popular fabrication method suited to the manufacture of light and stiff axisymmetric structures as the pressure vessels or the pipes. Strands of filaments impregnated with resin are wounded around a rotating mandrel by a translating guide that can move along one or more axes. The wrapped vessels are subjected to the autofrettage treatment: an internal pressure higher than (about 1.5 times) the maximum expected operating pressures applied to the tank to partially deform the metal liner over its elastic range.
The composite overwrap remains in its elastic range and, when the internal pressure is unloaded, tends to its original undeformed shape, inducing on the liner a compressive stress field. When it is applied the operative load, the stresses acting on the structure occurs to be lower than those obtainable without the autofrettage treatment.
Optimization loop is defined in order to find, for a given winding angle distribution, the minimum number of winding layers which are necessary in order to respect the structural constraints (reach maximum admissible stress in the central cylindrical portion of the vessel at burst pressure 900 bar) using an analytical model of the mechanical behavior of the pressure cylinder. The mechanical behavior of the optimal solutions will be tested using FEM models and experimentally.