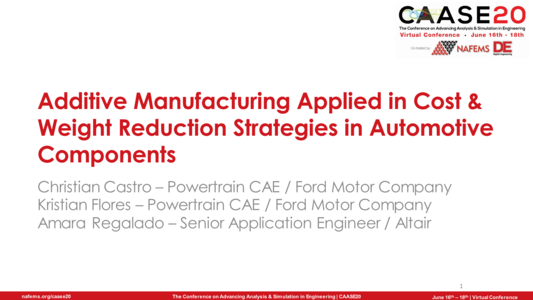
NAFEMS Americas and Digital Engineering (DE) teamed up (once again) to present CAASE, the (now Virtual) Conference on Advancing Analysis & Simulation in Engineering, on June 16-18, 2020!
CAASE20 brought together the leading visionaries, developers, and practitioners of CAE-related technologies in an open forum, unlike any other, to share experiences, discuss relevant trends, discover common themes, and explore future issues, including:
-What is the future for engineering analysis and simulation?
-Where will it lead us in the next decade?
-How can designers and engineers realize its full potential?
What are the business, technological, and human enablers that will take past successful developments to new levels in the next ten years?
Resource AbstractAs we know, Additive Manufacturing is a technology that allows the rapid fabrication of components via 3D printing. The process is so diverse (as it uses different materials and substances such as: metal powders, ceramics and plastics.) that it can be applied in several industries. This type of process is just ramping up in its applications as printers and materials are evolving at important rates.
There are two main reasons why this manufacturing method is rapidly gaining popularity:
1) 3D printers evolve rapidly and allow more complex components to be manufactured in less time, with less costs and with more innovative materials.
2) Just as the fuel saving approach has evolved the designs of automotive components to make them more efficient in weight and cost, we are now facing a second evolution of designs that aim to improve the efficiency of charge in batteries included in electric cars.
Explaining the details on the second point: we have detected a philosophy of "plasticization" of components that were previously made of steel, aluminum or different alloys. The new plastic components explore the possibility of building new geometries (more complex and more efficient) by means of topological and topographic optimizations but also to establish the bases that would allow these components to be manufactured by 3D printing methods.
This paper attempts to explain and exemplify how the Additive Manufacturing process can help not only to design components that are thought of as 3D printables but ones that are thought also in an intuitive, graphic and rapid process of structural optimization. This process, first, must be supported by software such as solidThinking Inspire, which allows the designer / engineer to go hand in hand in the design and implementation of rapid prototyping and printing components. All thanks to the fact that optimizations can be carried out by simulating the actual loading conditions of the system that is being designed.