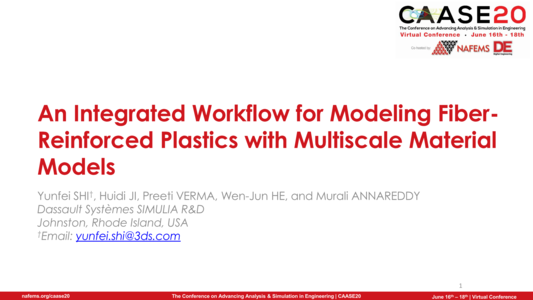
NAFEMS Americas and Digital Engineering (DE) teamed up (once again) to present CAASE, the (now Virtual) Conference on Advancing Analysis & Simulation in Engineering, on June 16-18, 2020!
CAASE20 brought together the leading visionaries, developers, and practitioners of CAE-related technologies in an open forum, unlike any other, to share experiences, discuss relevant trends, discover common themes, and explore future issues, including:
-What is the future for engineering analysis and simulation?
-Where will it lead us in the next decade?
-How can designers and engineers realize its full potential?
What are the business, technological, and human enablers that will take past successful developments to new levels in the next ten years?
Resource AbstractPlastic materials are used everywhere in our daily life for many good qualities, including light weight, low cost, durability, corrosion resistance, manufacturing versatility, and aesthetics. The usage of engineered plastics in the automotive industry has been trending up, with over 50% of the car interior now made of plastics. This is an inherited requirement of modern car designs for higher fuel efficiency and less carbon footprint. On the other hand, how to reduce plastic wastes and pollutions has become a pressing global challenge, which requires simulation-driven smart designs.
To increase the plastic strength and durability, chopped fibers are often added to the resin as stiffeners when plastic parts are injection molded. The mechanical properties of fiber-reinforced plastics (FRPs) often exhibit strong anisotropy and temperature-dependency, which largely depend on how fibers are oriented during thermal setting. When the injection gates and runner system are not carefully designed, manufacturing defects such as weld lines, air traps, and even short shots can be introduced and become weakness spots. If the part is not properly cooled down before being ejected out of the mold, the thermal expansion effect can give rise to significant residual stress and cause severe part warpage. These issues pose unique challenges to the design and manufacturing of FRPs.
The mean-field homogenization (MFH) method has been proven an effective and computationally efficient approach for characterizing the mechanical behaviors of FRPs. By taking account of individual constituents’ material properties as well as the volume fractions, shapes, and orientation of the fibers, complex nonlinear material behaviors at the macroscopic level can be accurately characterized to predict structural behaviors under thermomechanical loads and assess potential risks of fatigue and failure. Instead of costly physical testing and experiments, injection molding simulation can provide accurate predictions of the fiber orientation distribution, ejection temperature, and residual stresses used for the MFH. However, the current industry process lacks an integrated end-to-end solution. In order to complete this process, various design and simulation tools are often required with manual data management across different platforms, adding unnecessary development time and costs.
To solve this industry challenge, an integrated workflow has recently been developed for modeling the FRPs with MFH method-based multiscale models. This workflow includes part and mold design, plastic injection molding simulation, and structural simulation, integrated through process automation. The plastic injection simulation results including fiber orientation distributions were used in the subsequent structural simulation for accurate characterization of material behaviors. The effects of part thickness and locations of injection gates on the structural warpage, stiffness, and strength were studied to achieve an optimal design. A simulation template was reused for the verification of design variants. This integrated workflow can help improve product quality, reduce development time and costs, and achieve more sustainable and eco-friendly plastic designs.