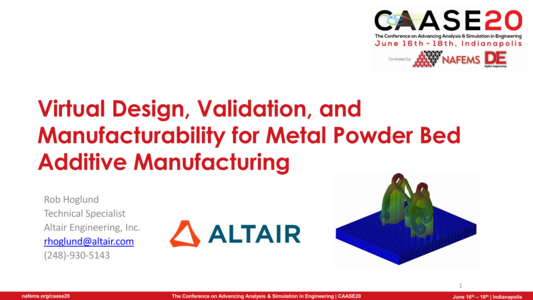
NAFEMS Americas and Digital Engineering (DE) teamed up (once again) to present CAASE, the (now Virtual) Conference on Advancing Analysis & Simulation in Engineering, on June 16-18, 2020!
CAASE20 brought together the leading visionaries, developers, and practitioners of CAE-related technologies in an open forum, unlike any other, to share experiences, discuss relevant trends, discover common themes, and explore future issues, including:
-What is the future for engineering analysis and simulation?
-Where will it lead us in the next decade?
-How can designers and engineers realize its full potential?
What are the business, technological, and human enablers that will take past successful developments to new levels in the next ten years?
Resource AbstractIn order to achieve cost-efficient and effective design of parts for production metal power-bed additive manufacturing, a variety of simulation tools have been proven useful and continue to improve. However, it is currently quite complex to develop a product for AM by validating structural performance, preparing the build, and predicting defects that might occur in the build process, moving from initial concepts to manufacturing feasibility studies. Engineers might use one software suite for topology optimization, one if they are interested in cleaning up the model; another for support generation, and even more for simulation to predict defects. Therefore, wide-ranging skill sets are required, whereas democratization of the workflows will enable faster product development in this space.
Crucial to designing for additive manufacturing (DFAM) is the ability to quickly modify CAD geometry, part orientation, and support structures early in the design phase. Efficient part design for AM involves eliminating overhanging regions where unnecessary, through optimization and other methods. Since extra support structures can add significant cost in both postprocessing and material usage, understanding the best part orientation and minimizing support structure usage is necessary to successful part design.
In addition to considering the supports and build direction, physics-based thermal and thermo-mechanical simulation can be used to understand manufacturing issues such as excessive distortion, residual stress, and final spring back. Macroscale simulation of the AM process, building a part layer by layer, can identify potential issues early on within the design process before any machine time or powder is committed.
In this study, an example is shown to design a part for additive manufacturing in one integrated environment, beginning with the original CAD model. Topology optimization and validation are carried out on this geometry, and the part is properly oriented and supported. Finally, thermo-mechanical simulation of the additive manufactured part is used to predict build defects and issues in the same environment and give feedback to the product designer. This methodology eliminates more potential for errors due to a higher number of data translations, reduces software licensing costs, and provides time savings. Integration of the validation and manufacturing simulation processes in the same environment can enable cost savings in the additive manufacturing product development process, as well as accelerate production timelines.