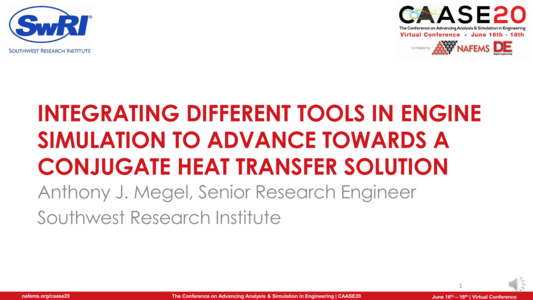
NAFEMS Americas and Digital Engineering (DE) teamed up (once again) to present CAASE, the (now Virtual) Conference on Advancing Analysis & Simulation in Engineering, on June 16-18, 2020!
CAASE20 brought together the leading visionaries, developers, and practitioners of CAE-related technologies in an open forum, unlike any other, to share experiences, discuss relevant trends, discover common themes, and explore future issues, including:
-What is the future for engineering analysis and simulation?
-Where will it lead us in the next decade?
-How can designers and engineers realize its full potential?
What are the business, technological, and human enablers that will take past successful developments to new levels in the next ten years?
Resource AbstractThermal management in internal combustion engines is an important factor impacting overall engine efficiency and emissions. Engine designs continue to push the capabilities of current hardware closer to their performance and durability limits. Effectively modeling heat transfer through various engine structures would give a thorough overview of engine performance and durability, which is pivotal during design and development. Therefore, more accurate and reliable analysis is necessary to ensure that designs are robust. Many CAE tools exist for various stages of analysis, including computational fluid dynamics (CFD), finite element analysis (FEA), and durability analysis. For engine design, these analyses may consist of combustion CFD, cooling CFD and thermal FEA, structural FEA, and fatigue. Even though many software vendors now offer tools to cover most of these analyses, often the integration of different tools is not straightforward, OEM’s utilize tools from multiple vendors, or consultants may operate with a combination of the customer’s tools and proprietary software. Transient analyses may require different time steps between systems, or in some cases transient and steady-state analyses can be leveraged together. In any case, interoperability between CAE tools must be established, validated, and standardized to achieve the improvements desired from analysis.
This research integrates multiple CAE tools to evaluate a method of conjugate heat transfer (CHT) analysis for both diesel and gasoline engines, combining in-cylinder combustion CFD, cooling jacket CFD, and engine thermal FEA with the aim of obtaining more accurate heat loss predictions and a more accurate temperature distribution in the engine than with existing analysis methods. Spray combustion CFD simulations were performed for the engines and results were validated with experimental data. FEA and cooling CFD simulations were performed in a separate software platform and final temperature measurements at various locations were compared with simulation results. Data interchanges between CFD and FEA software codes were performed at specified sub-cycle engine intervals and the simulations ran for multiple engine cycles. A comprehensive CFD-FEA conjugate heat transfer (CHT) methodology is proposed and the accuracy of this method is measured against existing analysis. Delivering more accurate simulation results allows engineers to better understand the thermal and mechanical behavior of structures and prevent the failure mechanisms that can occur in components that are continuously pushed to their limits.