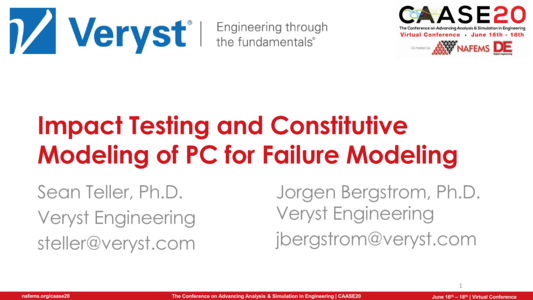
NAFEMS Americas and Digital Engineering (DE) teamed up (once again) to present CAASE, the (now Virtual) Conference on Advancing Analysis & Simulation in Engineering, on June 16-18, 2020!
CAASE20 brought together the leading visionaries, developers, and practitioners of CAE-related technologies in an open forum, unlike any other, to share experiences, discuss relevant trends, discover common themes, and explore future issues, including:
-What is the future for engineering analysis and simulation?
-Where will it lead us in the next decade?
-How can designers and engineers realize its full potential?
What are the business, technological, and human enablers that will take past successful developments to new levels in the next ten years?
Resource AbstractThermoplastic polymers are often used in impact protection applications in consumer products, athletic protection, manufacturing, aerospace applications, and the automotive industry. Engineers select thermoplastics due to their light weight, high strength, and significant energy dissipation during loading and unloading events. Accurate design for energy dissipation and impact protection during impact events requires advanced, high strain rate testing methods, advanced constitutive models, and material modeling techniques to characterize and capture the mechanical behavior for finite element modeling. This is complicated by the complex, non-linear, viscoplastic behavior of polymers.
Veryst Engineering has developed high strain rate testing techniques for advanced constitutive modeling of all polymers. We will present a study on the high strain rate testing and constitutive modeling of an impact modified polycarbonate (PC) material. We test the PC over 6 decades of strain rate in tension, compression, and shear, then calibrate the Three Network Viscoplastic (TNV) constitutive model to the data using MCalibration®. The TNV model is an advanced, viscoplastic material model that incorporates rate effects, pressure dependent yield, and damage to capture the complex behavior of thermoplastics, elastomers, and other polymers.
Thermoplastics typically exhibit pressure dependent failure that is characterized by the stress triaxiality at the failure point. This pressure dependence makes accurate failure modeling of material difficult and requires extra tests at different stress triaxialities. We test the material to failure at quasi-static rates at multiple stress triaxialities to capture this pressure dependent failure behavior of the material. We use an inverse calibration method with finite element models of the tests to calibrate the failure model. We then use the calibrated constitutive model in an explicit FE simulation in an impact scenario, and discuss the consequences of the choices in testing and material modeling. An accurate pressure dependent failure model has great consequence on accurate product simulation and accurate failure predictions.