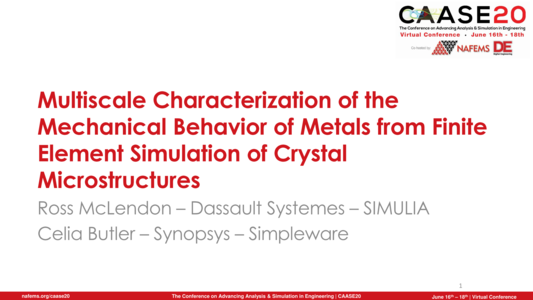
NAFEMS Americas and Digital Engineering (DE) teamed up (once again) to present CAASE, the (now Virtual) Conference on Advancing Analysis & Simulation in Engineering, on June 16-18, 2020!
CAASE20 brought together the leading visionaries, developers, and practitioners of CAE-related technologies in an open forum, unlike any other, to share experiences, discuss relevant trends, discover common themes, and explore future issues, including:
-What is the future for engineering analysis and simulation?
-Where will it lead us in the next decade?
-How can designers and engineers realize its full potential?
What are the business, technological, and human enablers that will take past successful developments to new levels in the next ten years?
Resource AbstractThe properties of metal alloys derive from the alloys’ microstructure, which itself is a product of the composition of the alloy and its manufacturing history, including temperature and work hardening among other factors. In general, this history will not be uniform across a component, especially in the case of welded components and components fabricated using newer advanced manufacturing techniques such as selective laser sintering. The metallurgical variability in a component can result in considerable spatial variability in the material behavior throughout a component. Furthermore, because of the broad variety of microstructures that could potentially arise, it may not be tractable to experimentally characterize every extant microstructure in a component.
Multiscale material modeling methodologies provide means to enable simulation of components with varying microstructure and capture process-structure-property relationships. First, simulation methods of manufacturing processes are able to predict the microstructure in a given region of a component based upon the time/stress/temperature history in a given region. Once the microstructure is determined, it is possible to utilize finite element simulations to predict overall material behavior of that microstructure. Based upon these microstructural simulations, nonlinear material models can be calibrated for application to longer length-scales. By varying these material models throughout the component, the effect of microstructural variability can be incorporated into the simulation of the component.
The work to be presented demonstrates the microstructure simulation and material model calibration aspects of this overall workflow using assumed microstructures and commercially available tools. Microstructural geometries will be assumed (rather than obtained from simulations of the manufacturing process), starting as voxel representations of a representative volume element (RVE) of the crystal microstructure. From this data, higher-fidelity finite element models of the RVE are developed using tetrahedral elements to more accurately represent the grain shapes. Following the development of these microstructural RVE meshes, nonlinear finite element analyses are performed on the RVEs using realistic representations of the nonlinear crystal behavior, such as crystal plasticity. These simulations/analyses are used to obtain the average stress-strain response of the microstructure under various load directions and histories, which is then used in a parametric optimization workflow to calibrate nonlinear phenomenological material models such as Hill plasticity to represent the complex microstructural behavior at the length scales of engineering components.