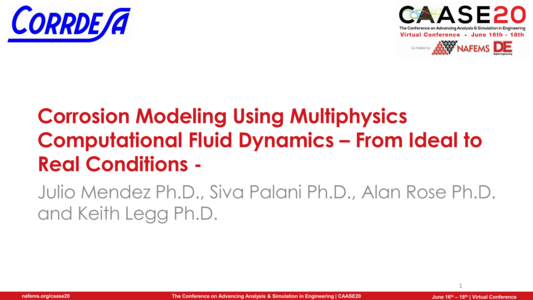
NAFEMS Americas and Digital Engineering (DE) teamed up (once again) to present CAASE, the (now Virtual) Conference on Advancing Analysis & Simulation in Engineering, on June 16-18, 2020!
CAASE20 brought together the leading visionaries, developers, and practitioners of CAE-related technologies in an open forum, unlike any other, to share experiences, discuss relevant trends, discover common themes, and explore future issues, including:
-What is the future for engineering analysis and simulation?
-Where will it lead us in the next decade?
-How can designers and engineers realize its full potential?
What are the business, technological, and human enablers that will take past successful developments to new levels in the next ten years?
Resource AbstractComputational Fluid Dynamics has been widely applied in different branches of thermal fluids, for example, combustion, turbulence, aerodynamics and more recently on aeroacoustics simulations. In this regards Direct Numerical Simulations (DNS) datasets have served the community very well in assessing the accuracy and/or credibility of these numerical applications. Unfortunately, one area that has not shown such a growth is corrosion modeling. The reason for this is the lack of accurate and robust electrochemical data (boundary conditions). Another important challenge is the large timescales involved in corrosion. Even ‘Accelerated’ Corrosion Tests (ACT) such as ASTM B117, and G85 salt spray chamber test often used to rank possible materials and coatings can take over a month. Despite these challenges, Multiphysics CFD packages are gaining popularity and some corrosion modeling applications are now found in the literature. The processes involved in corrosion are many and complex, however, one key parameter is the electrolyte film thickness which will clearly be different whether inside a chamber at high humidity with a continuous supply of sprayed saltwater compared to exposure from beach test where diurnal cycles result in a very thin electrolyte, of varying salt concentrations. However, most of the work shown in the literature is constrained to ideal conditions namely constant film thickness. In this sense, this work addresses two main areas, ideal and real conditions. On one hand, ideal conditions are relatively simple to asses, for example, we have developed two main procedures 1D and 2D methods, both name 1D and 2D Djinn® respectively. The former has been widely validated and verified while the latter is still in its developmental stage, but preliminary verification results demonstrate the accuracy of the code. These two tools considerably reduce the time needed to sort or test dozens or hundreds of different material/coatings combinations. On the other hand, the film thickness is also highly dependent on the geometry of the products and indeed their orientation. To this end, we implement fully 3D time-dependent Multiphysics CFD simulations on a multi-material structure along with the appropriate boundary conditions (polarization behavior of the materials involved) lead to an accurate variable film thickness that simulates the galvanic corrosion using the Laplacian potential model. The ultimate objective of this work is to correlate numerical tests (real conditions) with the ACT under realistic conditions and to demonstrate the advantage of using 1D and 2D numerical techniques to accelerate the initial stages of material and coating selection (ideal conditions). Preliminary results show that the numerical predictions agreed with the ACT results and ideal conditions are extremely efficient to down select material and coating options.