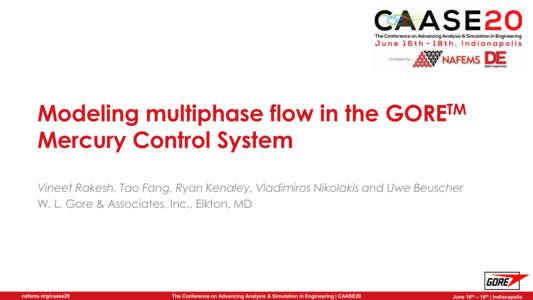
NAFEMS Americas and Digital Engineering (DE) teamed up (once again) to present CAASE, the (now Virtual) Conference on Advancing Analysis & Simulation in Engineering, on June 16-18, 2020!
CAASE20 brought together the leading visionaries, developers, and practitioners of CAE-related technologies in an open forum, unlike any other, to share experiences, discuss relevant trends, discover common themes, and explore future issues, including:
-What is the future for engineering analysis and simulation?
-Where will it lead us in the next decade?
-How can designers and engineers realize its full potential?
What are the business, technological, and human enablers that will take past successful developments to new levels in the next ten years?
Resource AbstractWith increasingly stricter mercury emissions requirements in several countries, effective technologies are critically needed for mercury removal from industrial flue gas. The GORE (TM) Mercury Control System (GMCS) provides a unique technology for elemental and oxidized gas phase mercury removal based on a Sorbent Polymer Catalyst (SPC) composite material while also facilitating sulfur dioxide (SO2) removal. The GMCS comprises of discrete stackable modules with an open channel structure for chemisorption of mercury from the flue gas to the SPC. SO2 in the flue gas is converted to sulfuric acid which is expelled from the hydrophobic SPC material to the channel surface, forms droplets, and flows counter-currently to the gas stream back to the scrubber. Additionally, a water rinse system is typically installed above and below the modules to help rinse acid and dust off the module surfaces. To understand these complex multiphase transport processes which can greatly affect the performance of the modules, we developed computational fluid dynamics (CFD) models in Simcenter STAR-CCM+. Volume of Fluid (VOF) method for tracking the air-liquid interface along with the unresolved Fluid Film model was used to model liquid generation and formation and movement of droplets in the flow channel. The model was used to study the influence of operating conditions and surface properties on the liquid flow on the channel surface. To model the rinse process, the VOF and Fluid Film models were further coupled with the Lagrangian multiphase model to incorporate nozzle atomization and droplet impingement. The model was used to investigate the different design variables and estimate the rinse efficiency for different operating conditions to obtain insights for optimizing the system. Results from CFD model provided critical insights difficult to obtain from experimentation such as the prediction of droplet generation, droplet movement and coalescence, and changes in bulk flow due to the generated droplets.