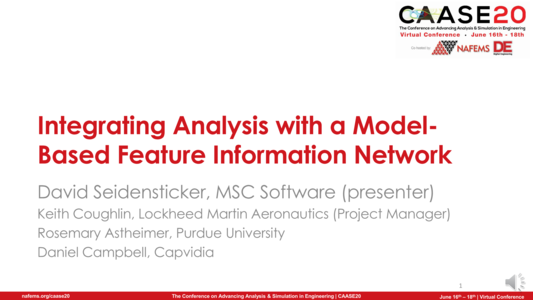
NAFEMS Americas and Digital Engineering (DE) teamed up (once again) to present CAASE, the (now Virtual) Conference on Advancing Analysis & Simulation in Engineering, on June 16-18, 2020!
CAASE20 brought together the leading visionaries, developers, and practitioners of CAE-related technologies in an open forum, unlike any other, to share experiences, discuss relevant trends, discover common themes, and explore future issues, including:
-What is the future for engineering analysis and simulation?
-Where will it lead us in the next decade?
-How can designers and engineers realize its full potential?
What are the business, technological, and human enablers that will take past successful developments to new levels in the next ten years?
Resource AbstractAnalysis engineers perform Computer-Aided Analysis (CAE) within the broader context of product design, manufacturing, and support. All the actors are highly interdependent, but connecting the design model and the material properties database to the finite element model (FEM) is typically a manual process assigned to the analyst, who gathers disparate inputs from other team members and incorporates them into the FEM. Similarly, once analysis is finished and the stress report is complete, manufacturing and support engineers must seek out the results from the analyst or a library of data, whether stored physically or electronically. They must then sift out the pieces of information that are relevant to their task, such as assessing nonconformances or designing repairs. There are opportunities for disconnects on both ends of this operation, and the sharing of data is a relatively labor-intensive operation.
To address this challenge, a Model-Based Feature Information Network (MFIN) was implemented by a diverse team of participants under the direction of MxD (formerly DMDII—Digital Manufacturing and Design Innovation Institute) as part of project 15-11-08. This project seeks to fill the industry need for a way to meaningfully capture and connect product information at the CAD feature level across all the various domains of manufacturing. Participating team members included end-users, technology providers, and leaders in academia, and the concept reflects the latest thinking on how MBE can be implemented effectively across multiple domains including Design, Analysis, Manufacturing, Quality, and MRO. The MFIN provides a conduit for the flow of information throughout the product lifecycle by establishing a data model and methodology for implementing Model-Based Enterprise (MBE) in a modern manufacturing environment. MFIN encourages process systematization and automation that allows manufacturers to create products faster with greater repeatable quality at lower costs. It also provides data traceability to enable meaningful advanced industrial data analytics, as well as to enable systematization and automation of business logic associated with manufacturing operations.
The integration of the FEM analysis into the MFIN framework will be shown here. This includes description of the mechanisms for passing geometry and material properties into multiple CAE software platforms and automatically creating associations between model features and the materials. After analysis is complete, the generation of standard results for review and consumption by other software will be demonstrated.