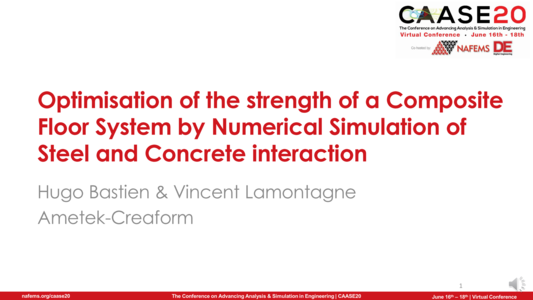
NAFEMS Americas and Digital Engineering (DE) teamed up (once again) to present CAASE, the (now Virtual) Conference on Advancing Analysis & Simulation in Engineering, on June 16-18, 2020!
CAASE20 brought together the leading visionaries, developers, and practitioners of CAE-related technologies in an open forum, unlike any other, to share experiences, discuss relevant trends, discover common themes, and explore future issues, including:
-What is the future for engineering analysis and simulation?
-Where will it lead us in the next decade?
-How can designers and engineers realize its full potential?
What are the business, technological, and human enablers that will take past successful developments to new levels in the next ten years?
Resource AbstractOptimisation of the strength of a Composite Floor System by Numerical Simulation of Steel and Concrete interaction
The use of composite beam structures in buildings advantageously combine compression strength of concrete and tension strength of steel. Deflecting as a single unit, a composite slab shows high stiffness and strength and is known to be the highest quality type of floor systems construction. More specifically, the CANAM Hambro composite steel joist system consists in composite T-beams, integrated in a transversally reinforced continuous slab. The bottom chord acts as a tension member, while bent rods serve as a web to resist vertical shear. The top chord withstands compressive loads prior to the addition of the concrete and act as a continuous shear connector between the steel and concrete in the composite system through adhesion and friction. Characterisation and optimisation of the adhesion and friction interface is believed to be one of the key factors to enhance the load-carrying capacity of the structure. In order to understand mechanics behind that interface, detailed Finite Element Models (FEM) were developed. The effects of specific features were studied independently in simpler localized FEMs, then correlated using physical testing. These FEMs were finally used to build a Global FEM taking into account all the different features to predict the entire structure performances.
To maximize the shear strength of the concrete-steel interface, a complex steel profile including localized features has been studied. A detailed FEM has been developed in LS-Dyna. Structural behaviour of concrete has been driven by a model previously developed for the automotive industry. Adhesion of concrete on steel, which might lead to a specific mode of failure of the structure has been represented using a tie-break contact. Steel frame with local geometrical feature has been represented in detail with its concrete surrounding by a high-density 3D mesh. This first model allowed to establish a first correlation of the algorithms used with the physical results and to study variations in localized geometrical features and frame cross-section. The loss of adhesion in shear on the concrete-steel interface has then been characterized and performance due the geometrical details in the frame has been optimized. This first FEM was correlated experimentally.
In addition to the effect of single design features, the behaviour of specific interfaces was studied. A second FEM has been developed to study a specific interface with a different failure mode. Plastic deformation of the steel and compression failure of the concrete were deemed to play a more important role in that interface rather than steel-concrete shear adhesion. Correlation with physical testing allowed to establish the critical parameters in the representation of that specific interface and demonstrated ability of the FEM to represent that second mode of failure; driver for a certain structure region.
Once the specific Finite Element Models were refined and correlated separately, the whole structure was modeled for the reproduction of the global performance test. The Global FEM, uniting the different techniques developed in the above-mentioned specific FEMs was meant to establish the load rating of the entire structure. The specific failure modes previously studied interact closely together in the global structure load-rating mechanical test. Failure load and load vs displacement predicted by the Global FEM were studied and showed to match closely the available test data. From that FEM, a better understanding of the different failure modes and their interaction was reached. Moreover, it consists of an interesting tool for optimizing the whole structure. Within that study, it has been possible to test different designs iterations and compare their performance without being dependent on costly physical testing.