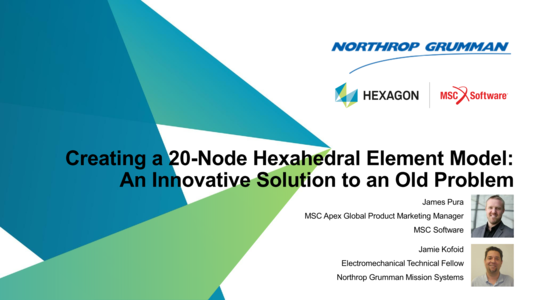
NAFEMS Americas and Digital Engineering (DE) teamed up (once again) to present CAASE, the (now Virtual) Conference on Advancing Analysis & Simulation in Engineering, on June 16-18, 2020!
CAASE20 brought together the leading visionaries, developers, and practitioners of CAE-related technologies in an open forum, unlike any other, to share experiences, discuss relevant trends, discover common themes, and explore future issues, including:
-What is the future for engineering analysis and simulation?
-Where will it lead us in the next decade?
-How can designers and engineers realize its full potential?
What are the business, technological, and human enablers that will take past successful developments to new levels in the next ten years?
Resource AbstractOne of the many critical analysis tasks in aircraft design is the evaluation of structural stability, and since the invention of finite element analysis (FEA), engineers around the world have been attempting to do this with as few elements (and thus lowest amount of computational hardware) as possible. One of those “sweet spots” between mathematically accurate results and lowest elements possible is the 20-node hexahedral element. Unfortunately, from a historical perspective, the process required to develop geometry suitable for a hexahedral mesh has been complicated and timeintensive – almost to the point of negating the time saved by faster solutions due to the hexahedral mesh. With the advent of MSC Apex’s hex meshing technological advancements, engineers now have a quick and innovative solution to their structural analysis workflows.
Ever since hex meshing was invented, comparisons have been made in many industries as to the accuracy of results between hexahedral elements and tetrahedral elements. Many prefer hex elements because the results are generally more accurate, but sometimes do not use them because of the extra cost (measured in engineering man-hours) needed to create them. Therefore, in certain situations, the accuracy of the simulation is sacrificed in favor of time saved. In certain circumstances, though, a high-quality hexahedral mesh is needed, and extra time is taken to develop this type of mesh in favor of the more accurate result.
Northrop Grumman Mission Systems in San Diego, CA is a leading global provider, manufacturer and integrator of advanced, secure and agile software-defined systems and solutions. The analysis group responsible for conducting this comparison commonly works on electronic assemblies & subsystems used in various air and ground applications.
The goal of this workflow evaluation was to conduct a 1-to-1 comparison of an already-completed workflow using Patran as the Pre-Processor and MSC Nastran as the solver. This same workflow was then completed using MSC Apex as the Pre-Processor with the same end goal – a successfully solved MSC Nastran finite element model. The comparison metric that was used during this evaluation was the time spent on each step of the pre-processing & solving workflow:
1. Geometric Defeaturing & Preparation for Meshing
2. Mesh Creation
3. Applying Loads & Boundary Conditions
4. Exporting Solver Deck to MSC Nastran (only needed during the MSC Apex comparison workflow)
5. Solving a Normal Modes Analysis using MSC Nastran
6. Solving a Linear Static Analysis using MSC Nastran
In summary, this paper describes the successful benchmark and evaluation of a Legacy hex meshing workflow using MSC Apex as a pre-processor to MSC Nastran, and the time savings achieved by implementing MSC Apex into this Northrop Grumman Mission Systems workflow. The two primary goals were to:
1. Simplify the workflow by reducing the number of tools necessary to complete the workflow.
2. Reduce the total amount of time needed to achieve the desired results.
Prior to this evaluation, this hex meshing workflow took approximately 18.5 hours. By utilizing the developments available in MSC Apex, this workflow was reduced to less than 8 hours, saving more than 10 hours each time this workflow is completed.