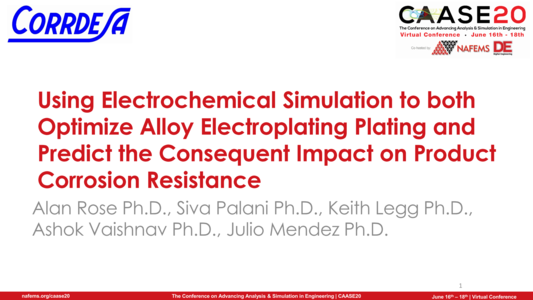
NAFEMS Americas and Digital Engineering (DE) teamed up (once again) to present CAASE, the (now Virtual) Conference on Advancing Analysis & Simulation in Engineering, on June 16-18, 2020!
CAASE20 brought together the leading visionaries, developers, and practitioners of CAE-related technologies in an open forum, unlike any other, to share experiences, discuss relevant trends, discover common themes, and explore future issues, including:
-What is the future for engineering analysis and simulation?
-Where will it lead us in the next decade?
-How can designers and engineers realize its full potential?
What are the business, technological, and human enablers that will take past successful developments to new levels in the next ten years?
Resource AbstractFor decades the aerospace industry have employed cadmium coatings for sacrificial corrosion protection of components fabricated from high-strength steels and aluminum alloys. However, cadmium is toxic and is no longer permitted on many products. Consequently, a substantial effort has been invested in the development, testing, qualifying and implementation of alternative coatings. One alternative for cadmium is zinc-nickel (ZnNi) which is of course an alloy and presents a manufacturing/processing challenge as we now have to control, not only the thickness of the electroplated ZnNi, but also the composition of each element as this is critical to the performance of the resulting sacrificial corrosion protection. So, the electroplating of the ZnNi layer has a significant impact on the life and durability of the finished component. This is particularly important for global industries that have their components coated by many different suppliers, so it is essential for the OEMs to understand how operational differences across the supply chain can affect corrosion and safety of their products – this can now be assessed computationally.
It is interesting (and fortunate) that the science of electrochemistry is relevant not only to the assessment of corrosion but also the process of electroplating. Using examples, this paper presents a workflow within a 3D framework that enables a designer to develop a corrosion risk map of a component/sub-assembly as a consequence of not only the material properties and operating environment but also the way in which it will be processed when the electroplated coating is applied.
Computational simulation tools have been used for decades in the areas of structures, fluid flow, heat transfer etc. The enabling factor for the utility of these tools is data – it is relatively straight forward to find structural and thermal material data. However, the existence of robust, consistent electrochemical material data is slim, which is a major reason for the slow uptake of electrochemical process modeling such as corrosion, electroplating, etc. Consequently, over recent years protocols for the acquisition of the critical electrochemical data have also been developed, enabling the construction of an electrochemical database for corrosion simulation.
Computational corrosion prediction will become a new discipline in the coming years, this paper will introduce some of the science and present initial verification & validation cases.