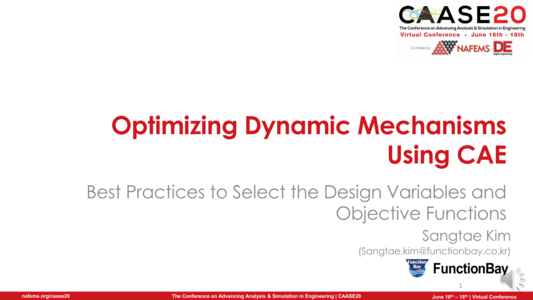
NAFEMS Americas and Digital Engineering (DE) teamed up (once again) to present CAASE, the (now Virtual) Conference on Advancing Analysis & Simulation in Engineering, on June 16-18, 2020!
CAASE20 brought together the leading visionaries, developers, and practitioners of CAE-related technologies in an open forum, unlike any other, to share experiences, discuss relevant trends, discover common themes, and explore future issues, including:
-What is the future for engineering analysis and simulation?
-Where will it lead us in the next decade?
-How can designers and engineers realize its full potential?
What are the business, technological, and human enablers that will take past successful developments to new levels in the next ten years?
Resource AbstractSystem optimization is a primary goal of CAE simulation. To optimize the design or performance of the system, there are many kinds of optimization methods and optimization software. However, many engineers still have difficulties in using these approaches to optimize their systems.
One of the reasons which makes optimization difficult is that too many trials (simulations) are required to optimize the system. The other reason is that many engineers are not familiar with the best types of inputs that should be used to define design variables and what types of outputs should be defined as objective functions of the system.
This presentation will introduce several simple but practical examples such as construction equipment (a wheel loader), deployment of a solar array for a satellite, unicycle dynamics while in operation, and a hand press. All of these models will be optimized using software that is based on the progressive meta-model method. Please note that the examples introduced here are dynamic mechanisms and that the transient behavior of the multibody system is optimized. This method optimizes the transient multibody system with a minimum number of trials.
The major topic of this presentation is to introduce best practices for deciding the design variables and the objective functions of a mechanical system for optimization. Each example has a different type of goal, for example to minimize the fatigue of the operator who use the hand press or to maximize the safety of the wheel loader. To achieve these goals appropriate inputs are set to the design variables and the objective functions to be optimized are defined. Then the optimization method is applied to the multibody simulation of these examples and the optimized results will be illustrated.
These examples demonstrate the need for optimization and provide the ideas and insights about how to optimize practical mechanisms.