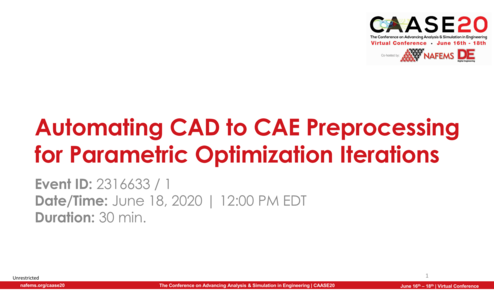
NAFEMS Americas and Digital Engineering (DE) teamed up (once again) to present CAASE, the (now Virtual) Conference on Advancing Analysis & Simulation in Engineering, on June 16-18, 2020!
CAASE20 brought together the leading visionaries, developers, and practitioners of CAE-related technologies in an open forum, unlike any other, to share experiences, discuss relevant trends, discover common themes, and explore future issues, including:
-What is the future for engineering analysis and simulation?
-Where will it lead us in the next decade?
-How can designers and engineers realize its full potential?
What are the business, technological, and human enablers that will take past successful developments to new levels in the next ten years?
Resource AbstractIn the current engineering environment, time to market is critical to develop and maintain market share. Not only do products need to be functional, they must achieve mass, cost, manufacturing and complex performance targets. This requires optimization methodologies that utilize CAE simulations extensively.
Recent studies indicate that 38% of CAE simulation project time is allocated to preprocessing. This consists of CAD model repair, meshing, contact definition, material properties application, boundary condition and load assignment. Often, this presents a substantial obstacle to quick evaluation of new design proposals. But more importantly, lack of automated CAD2CAE (CAD to CAE) automation presents a substantial obstacle for parametric design optimization tools such as HEEDS.
For example, automotive BiW (Body in White) CAE simulations require extensive preprocessing which can take days to weeks to develop the required finite element model (FEM). However, any changes to structure, bolts or welds, require substantial manual CAE preprocessing rework to the mesh, connectors, boundary conditions and loads. This prevents traditional parametric optimization codes from running automated DOEs to generate a response surface of different design configurations. As a result, such labor-intensive CAE models are rarely used in extensive optimization studies.
In this new approach, CAD model attributes drive automation protocols in the CAE environment. Mesh density, mesh element type, mesh quality, thickness, mid-plane extraction, spot welds, contact surfaces, boundary conditions and loads are embedded in the CAD model attributes. Upon CAE automation, these attributes are extracted and trigger the necessary CAE preprocessing recipes to ready the model for solution. What would take days to weeks long to manually complete, is contained within hours. More importantly, this allows for more design iterations as the parametric CAD models can be manipulated to resolve performance problems, and quickly re-assessed. Case studies demonstrate that such a process leads to improved product performance and quality.
This presentation reviews new methodologies and strategies in use at Siemens Digital Industries Software that automate many critical aspects of CAE preprocessing. Embedding critical information into the CAD model and CAE preprocessing scripts such as metadata and attributes that provide the right level of knowledge that enables automation. New advanced meshing capabilities achieving first time finite element quality targets further enables automated CAD2CAE. Other advanced features such as automated robust mid-plane surface development, spot weld joints, bolted joints, multi-point constraints, contact surface generation, automated load and boundary condition definition are critical contributors within the Siemens PLM NX CAD and Simcenter capabilities to achieve the final goal – automated CAD2CAE. These capabilities have demonstrated reductions in preprocessing time up to 97%. This represents a new frontier in democratizing CAE and enabling optimization for engineering.