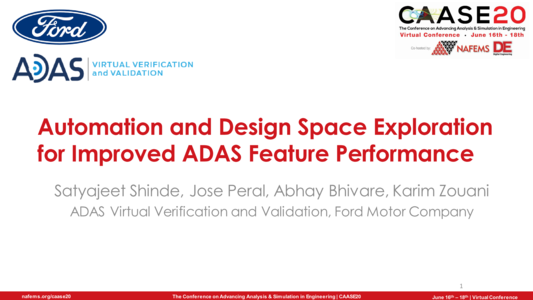
NAFEMS Americas and Digital Engineering (DE) teamed up (once again) to present CAASE, the (now Virtual) Conference on Advancing Analysis & Simulation in Engineering, on June 16-18, 2020!
CAASE20 brought together the leading visionaries, developers, and practitioners of CAE-related technologies in an open forum, unlike any other, to share experiences, discuss relevant trends, discover common themes, and explore future issues, including:
-What is the future for engineering analysis and simulation?
-Where will it lead us in the next decade?
-How can designers and engineers realize its full potential?
What are the business, technological, and human enablers that will take past successful developments to new levels in the next ten years?
Resource AbstractThe rapid growth of Advanced Driver Assist Systems (ADAS) is presenting many challenges to the automotive development engineers. On one hand, the development of the ADAS features requires an in depth knowledge of the desired customer experience. In fact, not only the performance of these features is becoming a differentiator between the different OEMs and customer usage data reveals a lack of satisfaction with the operation of certain ADAS features. On the other hand, the validation of these features requires advanced MBSE methods as it cannot rely solely on physical testing due to the significant number of scenarios required for the validation.
As an alternative to physical testing, simulation and virtual validation methods appear to be the tools of choice for the development of complex ADAS features. For example, the Fully Assisted Park Assist feature (FAPA) can be validated based on scenarios defined by a specific corporate validation test procedure. Typically, the scenarios involve an ego vehicle, moving at a speed below 30 Km/h, and different parking slot scenes such as between two cars or between a car and a curb. The key parameters monitored during the FAPA validation are the number of turns, the backward and forward steps, the final parking position and the time to park. It is obvious that in real world situation, there is a significant variation in the parameters that define the parking spot and the vehicle being parked. These variations result in significantly larger number of possible scenarios compared to what is defined by the standard validation test. Consequently, simulation is the only way to assess the performance of FAPA under the real world situations.
The MBSE simulation of FAPA requires the modelling of ultrasonic sensors, parking logic, vehicle dynamics, steering and powertrain. Customers exhibited some initial excitement using FAPA, but the long term customer satisfaction depends on key performance indicators such as the time to park, number of turns to park and accuracy to park. These indicators can be improved by tuning various design parameters. However, this tuning depends on the scenario considered. The combined number of tuning parameters and parking scenarios becomes huge and requires a sophisticated optimization approach to develop the tuning that maximizes customer satisfaction.
This paper presents an analytical method to identify the tuning parameters for best FAPA performance. This method integrates MBSE simulation and optimization using FAST optimizer with a genetic algorithm. The genetic algorithm is used to create the required design space in order to perform a multi-objective optimization using a large number of design parameters and scenarios. Results of this optimization method are discussed and the performance of the optimized FAPA is compared to the current status.