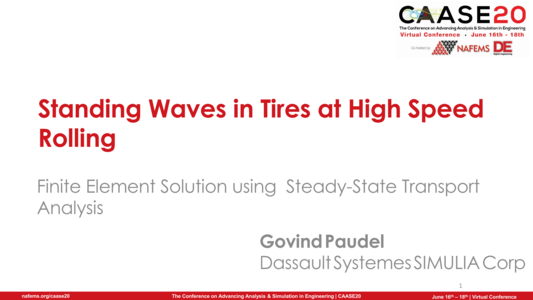
NAFEMS Americas and Digital Engineering (DE) teamed up (once again) to present CAASE, the (now Virtual) Conference on Advancing Analysis & Simulation in Engineering, on June 16-18, 2020!
CAASE20 brought together the leading visionaries, developers, and practitioners of CAE-related technologies in an open forum, unlike any other, to share experiences, discuss relevant trends, discover common themes, and explore future issues, including:
-What is the future for engineering analysis and simulation?
-Where will it lead us in the next decade?
-How can designers and engineers realize its full potential?
What are the business, technological, and human enablers that will take past successful developments to new levels in the next ten years?
Resource AbstractAlthough steady state tire analysis procedures have been long established in Abaqus, it has only recently become possible to simulate the development of standing waves at high rolling speeds. When standard Galerkin methods are used to evaluate inertial forces along streamlines, the solution diverges at high rolling speeds, becoming unstable at the onset of standing waves. A recent development in Abaqus steady-state transport analysis addresses this divergence problem by introducing a weighted shape function in the Galerkin methods. This improved shape function allows a non-uniform convection of the inertial forces along the circumference: from the leading edge to the trailing edge of the tire. As a result, convergence during high speed rolling can be achieved at and beyond the point where standing waves occur in the tire. This study demonstrates the analysis workflow for a P195/75R17 tire at rolling speeds up to 300 kph. The workflow follows standard tire analysis procedures: mounting, inflation, vertical load application, symmetric model generation, symmetric results transfer. The steady state rolling procedure requires identification of the free rolling condition of the tire, which was found by scanning a series of different rolling speeds until the tire's reaction moment about the axle becomes zero - neither braking nor driving. The solution is obtained on both flat and curved road surfaces. Starting at roughly 210 kph, standing waves are developed in the solution. Visualizations of the analysis results show standing wave effects in several aspects of the solution: displacement fields, stress / strain history and free rolling radius. The solution for the curved road surface exhibits a softer vertical stiffness and thus a smaller free rolling radius, so that greater displacements occur for a given vertical load. Intertial effects at high rolling speed are shown to produce large increases in the free rolling radius with a cross over between drum and flat cases at 270 kph.