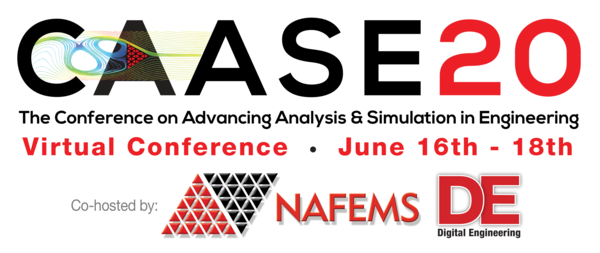
NAFEMS Americas and Digital Engineering (DE) teamed up (once again) to present CAASE, the (now Virtual) Conference on Advancing Analysis & Simulation in Engineering, on June 16-18, 2020!
CAASE20 brought together the leading visionaries, developers, and practitioners of CAE-related technologies in an open forum, unlike any other, to share experiences, discuss relevant trends, discover common themes, and explore future issues, including:
-What is the future for engineering analysis and simulation?
-Where will it lead us in the next decade?
-How can designers and engineers realize its full potential?
What are the business, technological, and human enablers that will take past successful developments to new levels in the next ten years?
Resource AbstractDigital Twin applications that integrate in-situ load measurements with periodically updated simulations of remaining fatigue life hold great promise for creating huge value in maintenance and logistical operations. In this work, we implement two commercially available, off-the-shelf solutions to create a closed-loop pogo stick digital twin that tracks damage accumulation due to actual loads experienced. A pogo stick was chosen because it experiences highly non-linear loading. The system records 12 strain gauges on the pogo stick frame at 1000 Hz. Strain gauges were placed using the True-Load load reconstruction. The True-Load process automatically creates strain correlation plots comparing measured strain to the strains in the FEA model simulated by the reconstructed loads. It also converts the strain gauge signals into 3 mutually perpendicular load channels that then are fed to a simulation of the pogo stick’s rubber tip. After each “operating” session, load history from the pogo stick is downloaded and accumulated as fatigue damage in a digital twin that tracks the remaining life of the rubber tip of the pogo stick. In order to accelerate loads processing to real-time speeds, the Endurica EIE interpolation engine has been used. EIE uses pre-computed finite element solutions of the rubber tip of the pogo stick under a series of load cases to rapidly convert input load history into strain tensor component history for each finite element. The Endurica DT incremental fatigue solver is then used to accumulate damage in all finite elements of the model, for each operating session. The result is a continually updated account of remaining life left in the pogo stick tip due to actual loads experienced. Whether you are developing a new product, or operating a digital twin, combining real-time high-accuracy structural loads with real-time fatigue evaluation software will propel you leaps and bounds towards a digital twin for durability.