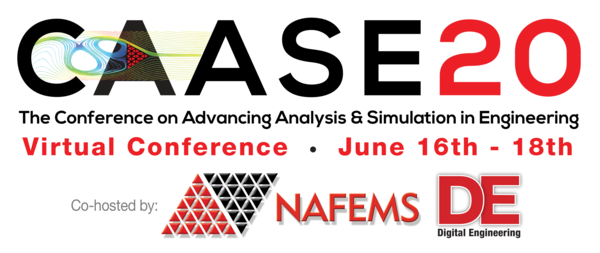
NAFEMS Americas and Digital Engineering (DE) teamed up (once again) to present CAASE, the (now Virtual) Conference on Advancing Analysis & Simulation in Engineering, on June 16-18, 2020!
CAASE20 brought together the leading visionaries, developers, and practitioners of CAE-related technologies in an open forum, unlike any other, to share experiences, discuss relevant trends, discover common themes, and explore future issues, including:
-What is the future for engineering analysis and simulation?
-Where will it lead us in the next decade?
-How can designers and engineers realize its full potential?
What are the business, technological, and human enablers that will take past successful developments to new levels in the next ten years?
Resource AbstractAs applications of computational methods to product development and manufacturing simulations mature, the demand for more accurate modeling of nonlinear material has steadily increased. The present work shows such a solution with a multiscale modeling approach for design and manufacturing applications involving granular media.
With increases in computing capabilities, there has been an exponential increase in usage of Discrete Element Method (DEM) for gaining dynamic insight for applications involving bulk solids. Fundamentally, DEM is suitable for low strain problems where the particle deformations are very small with respect to the particle size. So, while applications involving free surface flows like mixing, breakage, drying, coating, fluidized beds and etc. are very common, large strain problems like powder compaction remain a challenge for DEM. But compaction of granular media is an important process with applications to a broad spectrum of industries, namely food, chemical, geotechnical and pharmaceutical industries. Common examples include compression of multicomponent mixture of fine powders to manufacture pharmaceutical tablets, or compression of soil under varying moisture conditions. In practice, process understanding and optimization for such applications is driven by experimentation which often involves significant expenditure of time and material resources.
From a modeling perspective, the existing simulation methodologies attempt to model the material behavior with continuum methods like Finite Element Analysis (FEA). These approaches rely on constitutive laws such as the Drucker Prager class of material models, and are reasonably effective in capturing the material behavior when the degree of compaction is high - typical to the finished product state. However, these simulation techniques typically assume homogeneous initial conditions for the material properties such as density and zero initial stress conditions. Also, the existing FEA methodologies are not able to simulate the manufacturing process during which the material may have low compaction granular behavior, and the continuum methods are inapplicable.
The presentation will discuss a multiscale modeling technique where DEM simulates the initial stages of granular material compaction. Once the material compaction reaches a high degree as determined by the density of the material, density and the material state (stress, strain) are transferred as initial conditions to an FEA model. This continuum level simulation may address further compaction and/or operational loads on a finished product. Mapping properties from the DEM model into material properties and stress conditions are critical to the success of this approach. We discuss the challenges and practical considerations of the combined DEM+FEA approach as applied to a pharmaceutical application. The general methodology is valid for other applications in food, chemical and geotechnical industries.