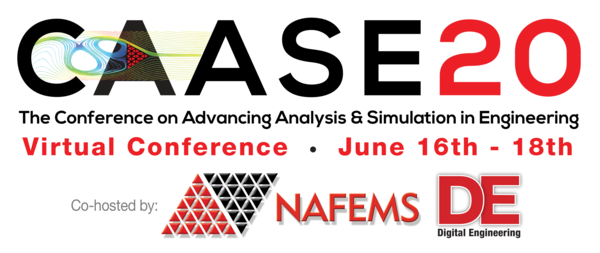
NAFEMS Americas and Digital Engineering (DE) teamed up (once again) to present CAASE, the (now Virtual) Conference on Advancing Analysis & Simulation in Engineering, on June 16-18, 2020!
CAASE20 brought together the leading visionaries, developers, and practitioners of CAE-related technologies in an open forum, unlike any other, to share experiences, discuss relevant trends, discover common themes, and explore future issues, including:
-What is the future for engineering analysis and simulation?
-Where will it lead us in the next decade?
-How can designers and engineers realize its full potential?
What are the business, technological, and human enablers that will take past successful developments to new levels in the next ten years?
Resource AbstractManufacturers are under continuous pressure to be competitive and get the most from their investments. The promise of digital simulation is a tremendous reduction in product development costs. But are companies realizing the full benefit of simulation?
This presentation explores a segment of the simulation lifecycle where much more can be gained. Simulation analyst productivity can be increased, product design collaboration can be greatly enhanced, and overall product quality can be improved by changing the way simulation information is shared across design, manufacturing, and supplier teams.
Ten to 15 years ago, pre-processing was the most time-consuming activity in the simulation lifecycle, but CAE vendors have made substantial improvements. In addition, solvers now run significantly faster due to an abundance of low-cost of computing power. These have resulted in a tremendous expansion in the volume of simulation results created. And companies continue to reduce test budgets in favor of simulation to qualify products.
During the same time, however, post-processing and simulation report creation have remained largely manual processes. This creates challenges not only for simulation analysts but for stakeholders like designers, release engineers, chief engineers, suppliers, and others who use simulation information and the product insights it provides.
Because these stakeholders cannot access simulation results directly, analysts must manually create reports of key simulation information to share with them. These reports are almost always created by cutting and pasting 2D static images or videos into PowerPoint or PDFs. Rather than providing interactive, model-based reports which stakeholders can query as needed, analysts must make educated guesses about which “snapshots” of information are needed by engineers and others.
This manual process becomes particularly challenging when analysts need to share design comparisons such as multiple iterations of a design, or comparing a slice against the full product, or even comparing multiple types of stress loads in a part. Creating comparative data or identifying design issues like hotspots is not only time-consuming, it introduces the potential for error.
In other words, stakeholders work with less than complete information, leading to poorer design decisions, lower productivity, and reduced product quality.
This paper outlines the potential for creating fully interactive, model-based, 3D simulation results reports with far less effort than is currently expended. These actionable simulation insights not only improve analyst productivity, they enable manufacturers to product higher quality products.