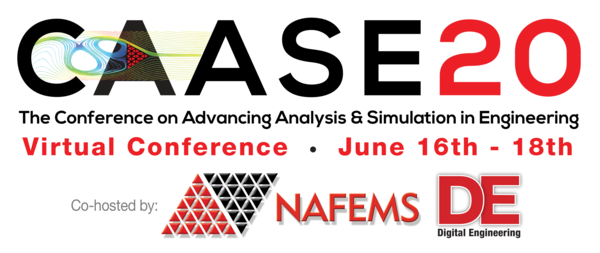
NAFEMS Americas and Digital Engineering (DE) teamed up (once again) to present CAASE, the (now Virtual) Conference on Advancing Analysis & Simulation in Engineering, on June 16-18, 2020!
CAASE20 brought together the leading visionaries, developers, and practitioners of CAE-related technologies in an open forum, unlike any other, to share experiences, discuss relevant trends, discover common themes, and explore future issues, including:
-What is the future for engineering analysis and simulation?
-Where will it lead us in the next decade?
-How can designers and engineers realize its full potential?
What are the business, technological, and human enablers that will take past successful developments to new levels in the next ten years?
Resource AbstractEngine cooling is a challenge across industries, such as Automotive and Industrial Equipment. Many equipment manufacturers focus mainly on meeting engine certification at a specific ambient temperature without realizing there is potential for additional airflow. A typical combustion engine generates a significant amount of heat, of which around 35% to 40% must be dissipated by the engine cooling system. The fan and fan shroud are critical components of the engine cooling system as they provide the necessary airflow through the engine radiator required to take the heat away from the coolant. In addition, the design of fan and fan shroud must meet packaging space requirements, which can increase the complexity of the cooling system. By maximizing the performance of fan and fan shroud, the cooling system can be improved through an increase in airflow, or a better distribution of the airflow across the radiator. Both improvements can lead to a reduction in fan speed, a reduction in fan power, longer operational life and possibly lower operating cost. Through exploration of a design space, leveraging optimization analysis, the impact of fan and fan shroud design parameters on the total airflow can be investigated to achieve optimal performance without constraining the design change to simple iterations from a baseline. This is even more critical when the equipment manufacturer is utilizing molded fan shrouds, as the optimal design must be achieved before implementing the costly initial mold tooling.With a better understanding of the key shape parameters early in the development schedule, the need for multiple tests and iterations late in the development schedule can be removed, reducing the number of molds to ideally just one.
In this study, a series of design of experiments and optimization of a fan and fan shroud were performed on an excavator to achieve maximum cooling airflow. The fixed design space for this engine cooling system covered design parameters such as tip clearance, fan to radiator distance, fan shroud depth and curvature and fan shroud ring depth. The performance of the system is assessed using a Lattice Boltzmann-based Method known for its best-in-class accuracy at predicting cooling performance. The final configuration of optimal design shows a 15% improvement to the initial one and illustrates how most machinery with similar configurations of fan and fan shroud can leverage such optimization approaches to help reduce total development time and cost.