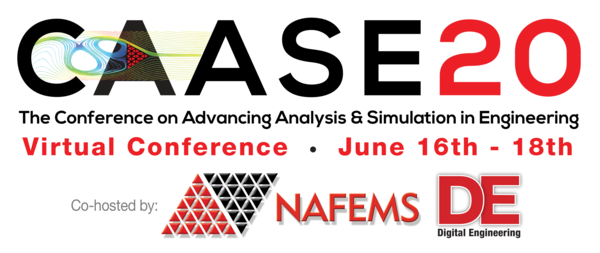
NAFEMS Americas and Digital Engineering (DE) teamed up (once again) to present CAASE, the (now Virtual) Conference on Advancing Analysis & Simulation in Engineering, on June 16-18, 2020!
CAASE20 brought together the leading visionaries, developers, and practitioners of CAE-related technologies in an open forum, unlike any other, to share experiences, discuss relevant trends, discover common themes, and explore future issues, including:
-What is the future for engineering analysis and simulation?
-Where will it lead us in the next decade?
-How can designers and engineers realize its full potential?
What are the business, technological, and human enablers that will take past successful developments to new levels in the next ten years?
Resource AbstractThe durability of a tire at high speed is strongly limited by the development of standing waves, due to effects on strain history, on viscoelastic self-heating, and on the temperature dependence of tire materials. In this work, we simulate a typical multi-step qualification test, including both the self-heating and damage development phenomena. The analysis is made using Abaqus to compute steady state structural and thermal solutions for each step of the test, and using the Endurica DT incremental fatigue solver to accumulate damage across all steps. Due to large temperature increases, material models were given as tabular functions of temperature. The fatigue law of the rubber compounds is particularly sensitive to temperature, with crack growth accelerating strongly at higher temperatures. The fatigue simulation utilizes critical plane analysis at each element centroid of the tire cross section. Strain history at each element centroid is obtained by following the material point streamlines defined in the steady state rolling structural analysis. Thermal transients during the testing procedure are treated approximately by breaking each test step into two sub-steps - a first substep using the thermal field from the immediately prior time step, and a second substep using the steady state thermal field from the current time step.
The simulation shows that standing waves are very damaging to a tire. Standing waves result in multiple fatigue cycles per tire revolution, which are addressed in the fatigue simulation by rainflow counting. Standing waves also lead to order of magnitude increases in self-heating and damage accumulation. They are indeed the major factor limiting the tire’s ultimate speed rating. Solutions are compared for a tire rolling on both flat and curved test surfaces, and for tires with and without a nylon overwrap layer. The trends in the solutions produced match expectation: durability on a flat surface is great than durability on a curve surface by approximately one letter grade, and nylon overwrap is shown to have a beneficial effect on the tire speed rating also.