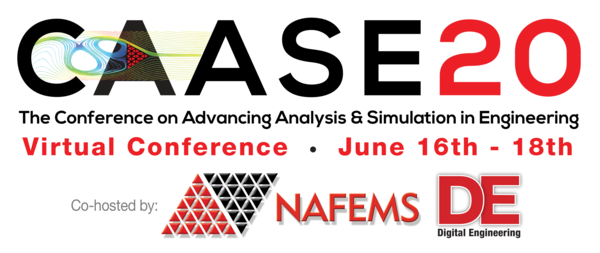
NAFEMS Americas and Digital Engineering (DE) teamed up (once again) to present CAASE, the (now Virtual) Conference on Advancing Analysis & Simulation in Engineering, on June 16-18, 2020!
CAASE20 brought together the leading visionaries, developers, and practitioners of CAE-related technologies in an open forum, unlike any other, to share experiences, discuss relevant trends, discover common themes, and explore future issues, including:
-What is the future for engineering analysis and simulation?
-Where will it lead us in the next decade?
-How can designers and engineers realize its full potential?
What are the business, technological, and human enablers that will take past successful developments to new levels in the next ten years?
Resource AbstractThe additive manufacturing (AM) industry continues to grow with new machines, faster processes and a large selection of materials. Lattice structures are used by nature and they are very effective for lightweight structural panels, energy absorption devices, thermal insulation, high performance heat exchangers, ballistic protection and porous implants. Design practitioners are now enabled to unleash the full potential of AM with the use of Lattice structures. A Taxonomy of Lattice Structures and an overview of the currently available generation techniques for on surface (i.e. triangle), 2 ½ D (i.e. honeycomb), 3D beam (i.e. Diamond, Octet) and 3D shell (i.e. Gyroid, Lidinoid) lattice structures will be presented.
Modern CAD and CAE tools can design, optimize and validate lattice structures’ performance. Since this all capability is available within integrated CAD and CAE environments, the designer reduces the product development time and increases confidence in the design.
For small number of the lattice structures a full geometry representation is sufficient for modeling and simulation. For medium number of lattice structures a simplified representation (beams and shells) is required. For large number of lattice structures a homogenization workflow is required. A demonstration of these techniques will be presented. A technique that explores the effectiveness of a typical lattice structure using the Geometric Efficiency Index will be also presented. The Geometric Efficiency Index is the ratio of stiffness reduction over the mass reduction. This technique uses homogenization to compute the Geometric Efficiency Index and enables the designer to select the most efficient lattice structure cell for the demand.
The Topology Optimization Process is used to reduce weight, maintain strength and improve thermal performance in 3D Printed Designs. The main bottleneck in this process was the conversion of topology optimization results back to CAD geometry. This presentation will demonstrate how to combine Sub-Divisional surface modeling, Topology Optimization and Lattice Structure generation tools to generate optimum designs. Examples of light weighting helicopter components using lattice structures and Additive Manufacturing will be presented.