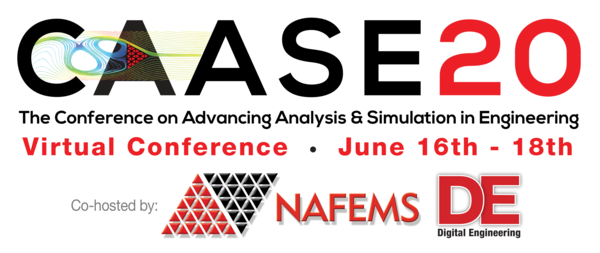
NAFEMS Americas and Digital Engineering (DE) teamed up (once again) to present CAASE, the (now Virtual) Conference on Advancing Analysis & Simulation in Engineering, on June 16-18, 2020!
CAASE20 brought together the leading visionaries, developers, and practitioners of CAE-related technologies in an open forum, unlike any other, to share experiences, discuss relevant trends, discover common themes, and explore future issues, including:
-What is the future for engineering analysis and simulation?
-Where will it lead us in the next decade?
-How can designers and engineers realize its full potential?
What are the business, technological, and human enablers that will take past successful developments to new levels in the next ten years?
Resource AbstractMost companies today use some form of Product Lifecycle Management (PLM) system to manage the data related to the products they design and deliver to their customers. These PLM systems are most often focused on managing the various pieces of information, including the relationships between each of the items, and providing access to personnel needing access to specific data. The format of the data contained within is determined by the application used to create it, but since the focus of these systems is most often human consumption, either directly or via the authoring software, the data is most often not easily interchanged between the systems where it is ultimately used.
While PLM systems allow companies to operate efficiently by making necessary information readily available, many realize that the data requires human involvement to move from one system to another. To reach the next level of efficiency and improve their competitiveness, world-class companies are striving to become “digitally connected enterprises” in which information can move easily between systems without extensive human involvement.
Such companies rely on the careful storage and usage of strategic information that can be widely accessed, contributed to, and understood by the various systems involved throughout the stages of a product’s lifecycle. To be successful, it is important not only to record information, but also to ensure that it is stored in formats that can be readily consumed.
A design engineer today, for example, may create many 3D models with visual annotations showing dimensions and tolerances that get shown on the associated drawings. Such visual data is important so that people involved in the creation and verification of the parts understand the requirements. However, this important information in this format is useless when creating the instructions for the machining or inspection systems.
To improve the effective use of the information, it must be created semantically (i.e. associated to the surfaces of the part to which it applies). It must also either be created in a format directly consumable by the downstream applications or automatically converted to a format that is understood while maintaining the integrity of the definition between the two data definitions. When done properly, the inevitable changes that occur during or even after the initial development process are quickly propagated to all systems involved in the production of the product.
It is also becoming more common to run simulations to predict product performance before an actual product or prototype is produced. Such simulations, when done properly and connected to the data, can also be used with data obtained from production to provide predictions of product performance without extensive, ongoing assembly-level testing during production. Today’s methods for recording inspection, however, typically don’t support this additional utilization of the simulation models. For example, functional gaging provides nothing more than pass/fail criteria for that individual part. Inspecting and recording part characteristics differently can support significantly more benefit. Ideally a digitally connected enterprise will connect the entire lifecycle of a product, from design, to manufacturing, to inspection, and back to design to support constant improvement.
This paper will discuss the effective use of information inside of a digital enterprise as it relates to inspection and simulation information. A connected enterprise needs to consist not only of relevant information, but meaningful data that can be used in future iterations of a product or process. Topics discussed will include today’s methods for recording inspection data, the usefulness of a connected enterprise, product-level simulations as it relates to performance, and how data, when not gathered correctly, can be a limiting factor across the enterprise.