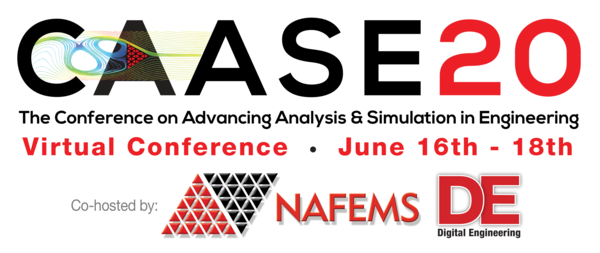
NAFEMS Americas and Digital Engineering (DE) teamed up (once again) to present CAASE, the (now Virtual) Conference on Advancing Analysis & Simulation in Engineering, on June 16-18, 2020!
CAASE20 brought together the leading visionaries, developers, and practitioners of CAE-related technologies in an open forum, unlike any other, to share experiences, discuss relevant trends, discover common themes, and explore future issues, including:
-What is the future for engineering analysis and simulation?
-Where will it lead us in the next decade?
-How can designers and engineers realize its full potential?
What are the business, technological, and human enablers that will take past successful developments to new levels in the next ten years?
Resource AbstractA single case study describing the utilization of topology optimization and the associated interpreted design process for the development of a functional piece of space flight hardware is described. The space flight hardware consists of a star tracker bracket as part of a larger altitude control system on the Spacecraft Bus, a multi-purpose platform housing many mission critical electronics, for the SWOT (Surface Water and Ocean Topography) spacecraft jointly built by NASA and National D'Études Spatiales (CNES). The case study corresponds to a redesign and manufacture of an existing bracket configuration that was failing under thermal and mechanical mission load cases. The existing bracket configuration has undergone topology optimization, implementing mission defined transient thermal, mechanical and dynamic joint load conditions to achieve a weight and performance optimized design only manufacturable via Additive Manufacturing (AM). After passing design verification by Finite Element Analysis, the component has been fabricated by a powder bed laser based fusion AM process.
The SWOT satellite observatory is a joint development by NASA and Centre National D'Études Spatiales (CNES) to effectively study how waves interfere. Using interferometry, or the study of how waves interfere, the SWOT mission will be NASA’s most accurate study of water measurement levels across the globe. This accuracy is achieved by a combination of a microwave radar system and several subsystems effectively working together to provide extensive radar data. This data is then used to create global maps of Earth's water levels, providing essential information on large rivers, lakes, and reservoirs – along with Earth's global ocean – at least twice every 21 days.
One such subsystem critical to the success of the SWOT mission is the Altimeter. The altimeter sends and receives signals that travel straight up and down from the Earth’s surface. Each pulse's round-trip travel time will be used to determine orbital height.
This paper focuses on the application of optimization from a pragmatic standpoint, addressing strict mission critical constraints with Altair OptiStruct’s unique multidisciplinary optimization workflow. In addition to the mission requirements and optimization routine itself, a thorough outline of the results interpretation associated with topology output and potential refinement will be discussed. This all occurring in the lens of utilizing the free form nature of Additive Manufacturing technology to achieve part complexity not achievable in traditional manufacturing methods.