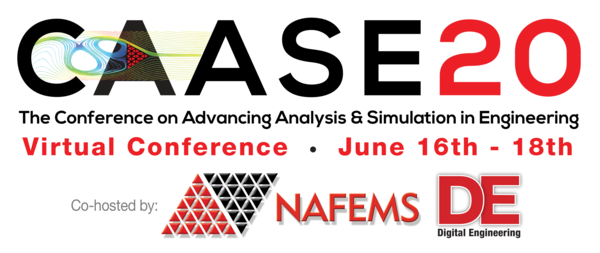
NAFEMS Americas and Digital Engineering (DE) teamed up (once again) to present CAASE, the (now Virtual) Conference on Advancing Analysis & Simulation in Engineering, on June 16-18, 2020!
CAASE20 brought together the leading visionaries, developers, and practitioners of CAE-related technologies in an open forum, unlike any other, to share experiences, discuss relevant trends, discover common themes, and explore future issues, including:
-What is the future for engineering analysis and simulation?
-Where will it lead us in the next decade?
-How can designers and engineers realize its full potential?
What are the business, technological, and human enablers that will take past successful developments to new levels in the next ten years?
Resource AbstractA new highly accurate and performant approach to finite element analysis (FEA) is to run simulations directly on smooth splines, the building blocks of computer-aided design (CAD) models. Thousands of academic papers have been published since 2005 investigating this new approach, and many significant advantages over traditional FEA have been reported. Recent applied research has shown that spline-based analysis promises game-changing industry benefits over traditional finite element analysis, including higher accuracy, greater robustness, and increased computational efficiency. These benefits are especially pronounced when running engineering simulations where high accuracy in the shape description is of great value, such as for contact or fatigue simulations. The implications to practical engineering design scenarios are profound.
The use of smooth splines for finite element analysis is a more efficient discretization method than using traditional FEA meshes. One of the reasons for this is that spline-based analysis employs the same functions that describe the geometry of the computational domain, while traditional FEA meshes are only an approximation of the geometry. The creation of analysis-suitable geometry using smooth splines is less time consuming, while the process for creating faceted meshes is often laborious and error-prone. Additionally, spines generally can represent the same geometry as FEA with significantly fewer elements, decreasing the time required to run the simulation.
This presentation will discuss the business and technical motivations for using spline-based simulation. Examples of how spline-based simulation can be integrated into commercial processes will be discussed, as well as an overview of how a number of industries are benefiting from spline-based simulation tools. We will also discuss the current research frontiers of spline-based simulation.
Attendees at this presentation will come away with an understanding of what spline-based simulation is and an appreciation of the fundamental improvement it might make to the simulation industry. They will also understand the current maturity of the technology and how they can access the technology today.