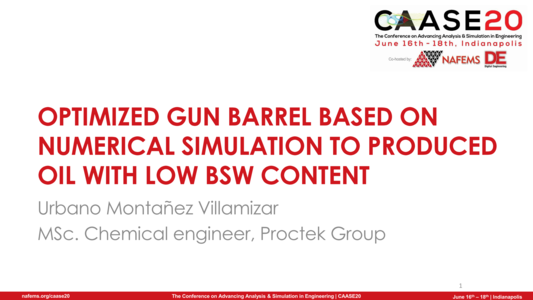
NAFEMS Americas and Digital Engineering (DE) teamed up (once again) to present CAASE, the (now Virtual) Conference on Advancing Analysis & Simulation in Engineering, on June 16-18, 2020!
CAASE20 brought together the leading visionaries, developers, and practitioners of CAE-related technologies in an open forum, unlike any other, to share experiences, discuss relevant trends, discover common themes, and explore future issues, including:
-What is the future for engineering analysis and simulation?
-Where will it lead us in the next decade?
-How can designers and engineers realize its full potential?
What are the business, technological, and human enablers that will take past successful developments to new levels in the next ten years?
Resource AbstractA gun-barrel separator, also called a wash tank, is the oldest equipment used for crude oil treatment. However, still in these days is one of the most used methods to break the oil-water emulsion and obtain oil with minimum specifications of water, salts, and sediments (BSW) before it is sent to a storage tank. Due to the gun barrels have been used for a long time, commonly these equipment do not reach the oil specifications or have low efficiency, therefore, the oil treatment process needs more stages to achieve the specific BSW limit for sale.
This work presents the methodology and results of the optimization of the internals (Inlet distributor, oil and water collectors) of a 20.000 barrel tank starting from an existing design. Computational fluid dynamics (CFD) was applied to simulate and evaluate the performance of various internals configurations. These simulations were conducted to determine the best configuration that ensures efficient separation of the oil-water mixture and oil with a low BSW content < 2% in the outlet. The simulations were carried out by Fluent commercial software under two-phase flow VOF model and k-ε realizable turbulence model.
The optimum inlet distributor has four “fish spine” with a total of 28 perforated branches. The water collector has also a “fish spine” configuration and the oil collector is a serrated perimeter weir in the upper part of the tank. The inlet distributor was simulated alone and distribution efficiency of 84 % and 71% for the two types of branches was achieved. The tank dimensions, and the orientation and level of the nozzles were considered to design the prototypes.
CFD simulations were conducted in the whole gun-barrel tank to compare the performance of the equipment with and without the distribution systems and fluid collection. For the first case, the effective retention time for the oil phase calculated through the discrete phase model (DPM) was 10.9 hours equivalent to 53% of tank utilization. On the other hand, for the tank without internal components, the effective retention time for the oil phase was 0.65 hour, which correspond to 3.2 % of the use of the tank. This result shows the importance of implementing flow distribution devices in separation tanks such as gun barrels.
Further CFD simulations were performed to evaluate the behavior of the gun barrel tank under different operating conditions (Several inlet flow rate) and to determine the maximum operation flow which allows obtaining the crude-oil with a maximum BSW content of 0.5%. From the simulation results, an operational curve (operating flow vs retention time) was constructed. This curve shows that when the inlet flow rate increases, the retention time decreases, but this is not a linear relationship. Subsequently, the retention times were crossed with bottle tests of the water-oil emulsion and an operating flow vs % BSW curve was created. This information helps identify the inlet flow rate based on the desired BSW content in the separated oil.