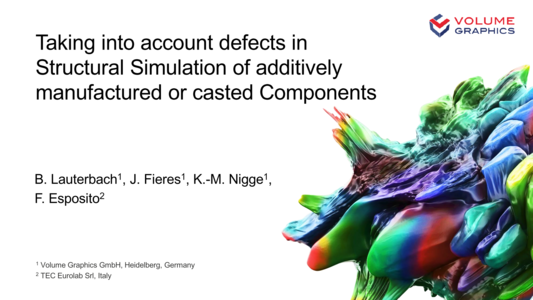
NAFEMS Americas and Digital Engineering (DE) teamed up (once again) to present CAASE, the (now Virtual) Conference on Advancing Analysis & Simulation in Engineering, on June 16-18, 2020!
CAASE20 brought together the leading visionaries, developers, and practitioners of CAE-related technologies in an open forum, unlike any other, to share experiences, discuss relevant trends, discover common themes, and explore future issues, including:
-What is the future for engineering analysis and simulation?
-Where will it lead us in the next decade?
-How can designers and engineers realize its full potential?
What are the business, technological, and human enablers that will take past successful developments to new levels in the next ten years?
Resource AbstractMicrostructural defects are inherent in additively manufactured or casted components. By optimizing the manufacturing processes, porosity might be reduced or shifted to non-critical regions, but avoiding porosity completely most often is not possible or leads to inefficient manufacturing processes. Therefore, to be cost-effective a certain amount of porosity has to be accepted.
By means of non-destructive testing, e.g. computed tomography (CT), pores in a structural component can be detected and quantified. Depending on their geometrical characteristics (e.g. shape and size) but also on their location within the component and the subjected loading, these pores might act as a source of stress concentration and reduce the load bearing capacity of the manufactured part. Therefore, it is desirable to include theses defects into a structural simulation. As there is very often a huge amount of microstructural defects, including them all in a structural simulation with FEM will create an enormous effort in FE mesh generation. It will result in a very large simulation models to resolve stress concentrations in the vicinity of each defect. While most of the defects will not affect the structural behavior of the component significantly, it would be sufficient to only include the critical defects in the FEM simulation. Thus, the simulation effort can be reduced significantly.
To sort the defects according to their severity, an accurate pre-simulation including all detected pores is necessary. This can be done efficiently with immersed-boundary finite element methods that do not work on geometry conform meshes. This approach is implemented in the Structural Mechanics Simulation module of VGSTUDIO MAX by Volume Graphics. It simulates local stress distributions for linear elastic material properties directly on computed tomography (CT) scans which accurately represent complex material structures and internal discontinuities. From the stress fields calculated by the immersed boundary finite element simulation, the critical pores can be identified. Using the volume meshing module in VGSTUDIO MAX efficient creation of a tetrahedral mesh on the CT scan taking into account only the critical pores can be done. Thus, the porosity information can be made accessible for classical FEM simulations making use of the wide range of functionalities that are offered by a fully capable finite element software (e.g. non-linear material models).
A workflow from CT scanning, analyzing most critical defects and efficient meshing to structural simulation with ANSYS maintaining the relevant features of the scanned object will be presented. It enables to evaluate deviations in the mechanical performance of the manufactured towards the designed component by simulation.