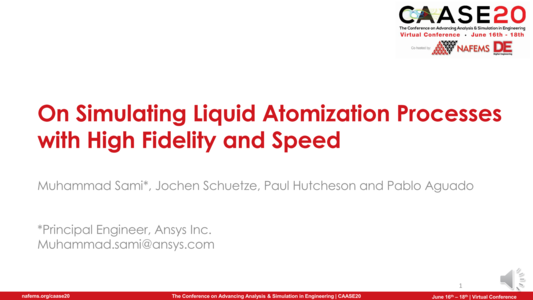
NAFEMS Americas and Digital Engineering (DE) teamed up (once again) to present CAASE, the (now Virtual) Conference on Advancing Analysis & Simulation in Engineering, on June 16-18, 2020!
CAASE20 brought together the leading visionaries, developers, and practitioners of CAE-related technologies in an open forum, unlike any other, to share experiences, discuss relevant trends, discover common themes, and explore future issues, including:
-What is the future for engineering analysis and simulation?
-Where will it lead us in the next decade?
-How can designers and engineers realize its full potential?
What are the business, technological, and human enablers that will take past successful developments to new levels in the next ten years?
Resource AbstractLiquid atomization is a necessary technique used in several industrial processes for a variety of reasons. The atomization nozzles are designed to maximize the efficiency of the process based on the objective at hand. The shape and atomization techniques vary across the board and it has become important to bring in sophisticated analysis tools to ensure the design meets the expected performance with least cost and reduced time to market. In achieving this goal, research and development departments are turning to Computational Fluid Dynamics to model complex internal nozzle hydrodynamics that includes resolving of multiple flow scales, cavitation, liquid/gas interface instabilities and liquid and gas compressibility. The modelling of these processes has been an active area of research for many decades. Currently, with high-performance computing , we have now reached a state where simulating complex atomization models is becoming more mainstream, evident by the increasing number of researchers in academics and engineers in industry running these detailed simulations.
This paper summarizes our experience with such detailed simulation of liquid atomization. ANSYS, Inc. has developed a hybrid model that combines the volume-of-fluid (VOF) model with the discrete-phase model (DPM) in Fluent 2020R1 to provide an efficient and robust tool to model primary atomization processes. This has been tested on several applications such as Simplex Nozzles, jet in cross flow (gas turbine applications) and impinging jets. There are several physical models and solver settings that make an impact on the fidelity and efficiency of the simulation. We describe the components of the integrated VOF-to-DPM model transition setup and present results from several simulations. Such simulations require robust modelling of turbulence, interface tracking, mesh adaption, model transition and parallel scalability. The purpose of this paper is to highlight key steps in the simulation and to provide guidance to others in setting up such simulations.