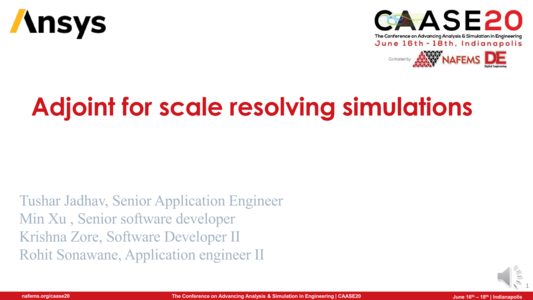
NAFEMS Americas and Digital Engineering (DE) teamed up (once again) to present CAASE, the (now Virtual) Conference on Advancing Analysis & Simulation in Engineering, on June 16-18, 2020!
CAASE20 brought together the leading visionaries, developers, and practitioners of CAE-related technologies in an open forum, unlike any other, to share experiences, discuss relevant trends, discover common themes, and explore future issues, including:
-What is the future for engineering analysis and simulation?
-Where will it lead us in the next decade?
-How can designers and engineers realize its full potential?
What are the business, technological, and human enablers that will take past successful developments to new levels in the next ten years?
Resource AbstractAdjoint is an optimization method popularly used for shape optimization in Automotive industry. In most of the commercial codes it has been developed to use steady state Reynolds averaged naiver stoke (RANS) solutions as a primal solution to adjoint. However, it is also has been observed that certain regions on a vehicle may have strong transient effect which are difficult to capture using steady state calculations. For example, the modification in rear spoiler, d-pillar modification or air dam can sometime produce large transient effects and the steady state calculations may not predict right tendency in drag benefit at these locations. In aerodynamic point of view these are important region in optimization perspective. The approach discussed here will require a fast-transient stress blended eddy simulation (SBES) followed by length scale evaluation from restricted RANS calculation and then adjoint optimization. The time averaged mean velocity field obtained from SBES calculation will replace RANS field prior to running adjoint calculations. The restricted RANS calculation will only solve for turbulent length scale and flow calculations will be frozen. This will require more computational power to resolve the smaller scales as compared traditional RANS based approach however it is more reliable as the drag benefit obtained from above mentioned design changes are typically very small, mostly less than 5% altogether.
In this work the process will be discussed using DrivAer car model and other simplified designs like Hyundai Simplified Mode (HSM) and SAE models for which the test data is available for initial design. The shape optimized designs will be compared for Steady and Transient scale resolving models. The DrivAer car model resembles to real car model and has aerodynamic shape. The HSM model is simplified but has sunroof window buffeting. It is quite difficult for steady state RANS to predict design change very accurately. The focus will be on optimizing the front roof region. The SAE body has a mirror which will be optimized for drag and the comparisons will be made between steady state adjoint and transient adjoint calculations. An ANSYS Fluent software will be used for Meshing, Solution and Postprocessing.
The HSM and SAE body case was originally developed to study external wind noise to interior cabin. However, the work will focus only on Adjoint shape optimization and understanding the benefit of using scale resolving simulation over steady state calculation.