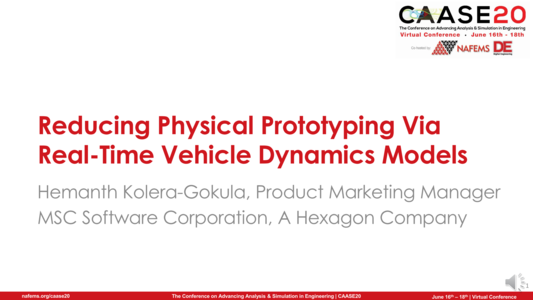
NAFEMS Americas and Digital Engineering (DE) teamed up (once again) to present CAASE, the (now Virtual) Conference on Advancing Analysis & Simulation in Engineering, on June 16-18, 2020!
CAASE20 brought together the leading visionaries, developers, and practitioners of CAE-related technologies in an open forum, unlike any other, to share experiences, discuss relevant trends, discover common themes, and explore future issues, including:
-What is the future for engineering analysis and simulation?
-Where will it lead us in the next decade?
-How can designers and engineers realize its full potential?
What are the business, technological, and human enablers that will take past successful developments to new levels in the next ten years?
Resource AbstractReal-time compliant vehicle dynamics models for HiL and DiL integration have traditionally involved a low number of Degrees of Freedom (DOF), typically around 20. Such models are typically used to characterize the behavior of the body via lookup tables. While these Reduced Order Models (ROMs) are a valid approach for some applications, compromising on the number of DOF’s is no longer a requirement for real-time computation.
Readily available high-performance computing and advances in engineering simulation techniques have now made higher fidelity real-time simulations possible, providing more valuable insights. Real-time simulations now provide an opportunity to connect physical components and virtual models in Hardware in the Loop (HiL) and Driver in the Loop (DiL) automotive test environments.
MSC Software has designed Adams Real-Time to preserve the topology and parametrics of the MBD-modelled system in real-time applications. This makes it possible to maintain elements such as hardpoints, joints, springs, dampers, and bushings and make modifications without the need to calibrate a new ROM for every change. As such, the model can capture higher frequency characteristics in the system responses, and different configurations can be introduced and explored with a shorter turnaround time. Adopting a one tool, one model approach for both real time and non-real time applications eliminates error-prone model translations between different tools. This approach also makes it possible to tune and optimize systems very efficiently and has the potential to remove weeks from a typical vehicle development program.
The Automotive industry is under constant pressure to address market demands in resource-constrained engineering environments. Stiff development timelines are compounded by shrinking physical prototyping budgets. The Ford Motor Company is focused on providing its customers with a world-class vehicle drivability and the ride comfort experience, which are critical attributes that drive a customer’s perception of vehicle quality. These critical attributes are in turn impacted by the transmission shift strategy.
The traditional approach to transmission calibration at Ford involved physical testing of full vehicle prototypes with extensive test schedules. This approach was both time consuming and expensive. In collaboration with MSC software and its services group, Ford developed a Hardware-in-the-loop testing process to reduce the need for physical prototyping. The HiL testing process has helped Ford meet its test objectives with fewer physical prototypes and in a lab environment that facilitates the tuning process. The same engine and transmission prototypes can be tested with multiple vehicles under multiple loading scenarios.
In this presentation the Adams Real time modeling paradigm will be presented and benefits from the approach will be detailed via the Ford case study.