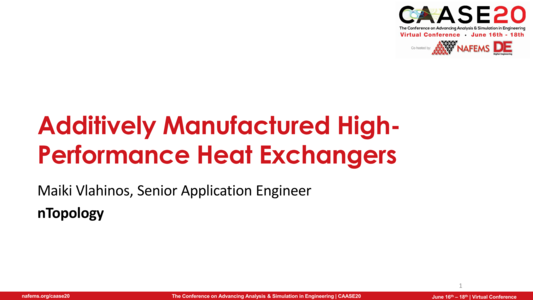
NAFEMS Americas and Digital Engineering (DE) teamed up (once again) to present CAASE, the (now Virtual) Conference on Advancing Analysis & Simulation in Engineering, on June 16-18, 2020!
CAASE20 brought together the leading visionaries, developers, and practitioners of CAE-related technologies in an open forum, unlike any other, to share experiences, discuss relevant trends, discover common themes, and explore future issues, including:
-What is the future for engineering analysis and simulation?
-Where will it lead us in the next decade?
-How can designers and engineers realize its full potential?
What are the business, technological, and human enablers that will take past successful developments to new levels in the next ten years?
Resource AbstractRecent advances in implicit geometry modeling are enabling design engineers to have complete control over geometry and develop complex periodic structures; that when coupled with advanced manufacturing techniques provide the opportunity to greatly increase performance in heat exchange applications. Specifically, triply periodic minimal surfaces, such as the gyroid, have several advantages. They can separate an otherwise single domain volume into two different and independent yet continuous regions. These periodic structures inherently provide a large surface for the minimum amount of material within a defined boundary. They smoothly intermingle the two independent regions, the cold and hot fluid domains, maximizing the surface area contact while reducing pressure drop within the fluid passages. Lastly, the gyroid and other minimal surface lattices do not require any support structures during the additive manufacturing process. Together, these unique geometry characteristics make minimal surface topologies ideal for enclosed volumetric infills for not only improving the thermal performance of heat exchangers but light-weighting the unit as well. Coupled with advances in additive layer manufacturing, improved additive materials can aid in the increased performance of a heat exchanger. Specifically, the use of cutting edge high strength aluminum alloys enable thinner walls that maximize heat transfer and increase fluid volume while maintaining the ability of the heat exchanger to meet structural integrity requirements.
The improved thermal capacity and heat transfer of a heat exchanger with a triply periodic minimal surface structure internal to the heat exchanger structure will be demonstrated. This presentation will include documentation of the design process, iterations, analysis tools and results of integrating advanced CAD, CAE, and CFD tools used to design, validate, and manufacture a representative fuel cooled oil cooler for aerospace applications.
Learning Objectives
Demonstrate how triply periodic minimal surface structures can greatly enhance heat exchanger performance through the use of an advanced implicit geometry kernel in conjunction with traditional CAE and CFD tools.