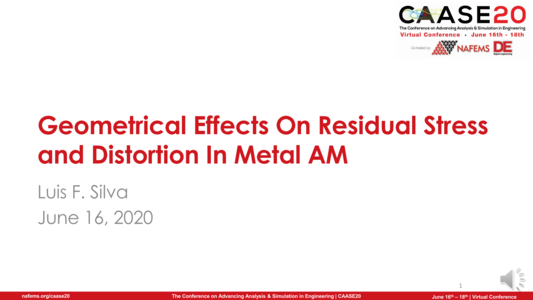
NAFEMS Americas and Digital Engineering (DE) teamed up (once again) to present CAASE, the (now Virtual) Conference on Advancing Analysis & Simulation in Engineering, on June 16-18, 2020!
CAASE20 brought together the leading visionaries, developers, and practitioners of CAE-related technologies in an open forum, unlike any other, to share experiences, discuss relevant trends, discover common themes, and explore future issues, including:
-What is the future for engineering analysis and simulation?
-Where will it lead us in the next decade?
-How can designers and engineers realize its full potential?
What are the business, technological, and human enablers that will take past successful developments to new levels in the next ten years?
Resource AbstractAdvancements in metal additive manufacturing have made it a viable solution for the rapid prototyping and manufacturing of complex structures. However, the associated part deformation may cause unacceptable dimensional deviations and the accompanying residual stresses may cause premature failure or otherwise weaken the overall structure. Such stresses occur due primarily to large temperature gradients in the additive manufacturing processes such as selective laser sintering (SLS). An accurate and computationally efficient prediction of these effects is desirable for part geometry optimization that incorporates the manufacturing process.
The proposed manuscript will model the particle nature and the micro-structure of the metal powder using the generalized method of cells (GMC) coupled with time-dependent thermo-mechanical finite element methods. This coupling will occur via user subroutines to a finite element software. The generalized method of cells is capable of accounting for many material constitutive relationships, including visco-elasto-plastic models (Bednarcyk, 2002). In addition, the effects of geometrical features on residual stresses and deformations will be studied. Subsequently, experimental validation studies on the simulation results will be conducted. It is expected that the discontinuities due to a geometrical feature, the particle-to-particle interaction, and the evolving micro-structure impact the overall part deformation and residual stresses.
The generalized method of cells uses a repeating unit cell to represent the micro-structural domain of the heterogeneous material or composite. Each repeating unit cell can then have sub-cells that may represent different phases or materials in a composite. The computed stress and strain of each sub-cell can then be used to compute the effective homogenized response (stress/strain, thermal/mechanical material properties) of the repeating unit cell (Aboudi, 2012). These effective properties will be used as the constitutive model in the FE simulation, effectively cascading the micro-structural response onto the macro-scale.
The unique contributions to be reported in the manuscript include the effects of an evolving porosity on residual stresses and deformations. In addition, this work will demonstrate how basic geometrical features affect the residual stresses in SLS 3D printing. The trends with the additional geometrical features will be studied in this manuscript. This work will be a segment in a larger project aimed at minimizing the residual stresses and deformations in additive manufacturing.