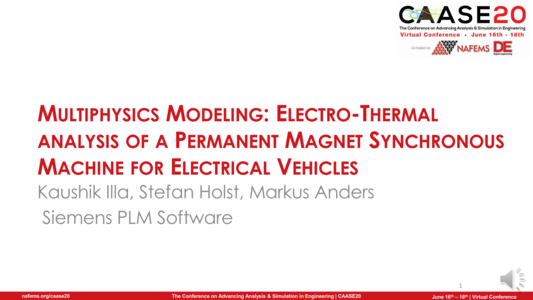
NAFEMS Americas and Digital Engineering (DE) teamed up (once again) to present CAASE, the (now Virtual) Conference on Advancing Analysis & Simulation in Engineering, on June 16-18, 2020!
CAASE20 brought together the leading visionaries, developers, and practitioners of CAE-related technologies in an open forum, unlike any other, to share experiences, discuss relevant trends, discover common themes, and explore future issues, including:
-What is the future for engineering analysis and simulation?
-Where will it lead us in the next decade?
-How can designers and engineers realize its full potential?
What are the business, technological, and human enablers that will take past successful developments to new levels in the next ten years?
Resource AbstractWith the emergence of electric vehicles (PHEV, MEV, BEV and FEC) and the significant reductions of permanent magnet material and its related cost, new challenges arise. In particular, the design of electric machines smaller in size and weight along with higher torque and power density needs better cooling to not overheat. This implies a strong need of multi-physic analysis, namely electro-magnetic in combination with thermal.
The loss and temperature distribution in an electric machine in operation can be assessed early on in the design process using simulation methods (virtual prototyping). In this paper, we present a multi-physics modelling of the electromagnetics together with conjugate heat transfer and flow thermal outputs in one environment, running in parallel. A loosely coupled electromagnetic and thermal analysis is performed to obtain the overall machine performance. An interior permanent magnet (IPM) synchronous machine was selected, as they take advantage of the reluctance torque lowering the need of permanent magnet material. This is applied to xEV application.
The design process of the machine usually begins with the geometry creation. This is done in Simcenter SPEED. This is where the control parameters are defined for example, the current, the voltage, the circuit regulation topology, phase advance angles for the electromagnetic characteristics and density, specific heat, conductivity of active materials for thermal characteristics and other parameters which are essential in defining the machine. The SPEED model is then imported into STAR-CCM+ where the objective is to calculate the over an electric cycle averaged iron loss distribution which is also temperature and load dependent. In this paper we present a novel approach using a finite element discretization technique for a 3D section of an electric machine and obtain the magnetic field and loss distribution and exchange the data with the full 3D CFD thermal model in one environment of STAR-CCM+ linked by the new feature Simulation Operations, which eases the linking of multi-physics simulations significantly. Additionally, with a new approach in driving SPEED from STAR-CCM+ we are able to work from a sole environment – no need to switch between different tools.