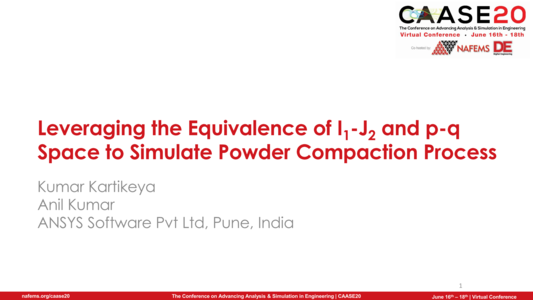
NAFEMS Americas and Digital Engineering (DE) teamed up (once again) to present CAASE, the (now Virtual) Conference on Advancing Analysis & Simulation in Engineering, on June 16-18, 2020!
CAASE20 brought together the leading visionaries, developers, and practitioners of CAE-related technologies in an open forum, unlike any other, to share experiences, discuss relevant trends, discover common themes, and explore future issues, including:
-What is the future for engineering analysis and simulation?
-Where will it lead us in the next decade?
-How can designers and engineers realize its full potential?
What are the business, technological, and human enablers that will take past successful developments to new levels in the next ten years?
Resource AbstractPowder compaction is an important step in pharmaceutical tableting process. It is also used in fuel, automotive and ceramics industry. Aim of compaction is to attain desired shape and enough ‘green strength’. Attaining a minimum and near uniform green strength is critical for the part to successfully endure downstream handling loads till the sintering stage, where the part attains its full strength. Inhomogeneous density distribution is seen to be related to tablet failures like capping, lamination, sticking, crack, chip off, etc. If this happens in production environment, it can lead to significant losses and delays. Compaction of granular materials is performed using Extended Drucker Prager material model with cap(EDPC). Experimental data is in terms of pressure & von-Mises stress. EDPC is defined in terms of the basic invariants I1 and J2. The experimental quantities are mostly in the form of p-q (pressure and von-Mises stress) space. Many of the commercially available simulation software packages have the Extended Drucker Prager material model with cap in terms of invariants i.e. in the I1-J2 space. Thus conversion of parameters from p-q space to I1-J2 space is required. The present work demonstrates the use of equivalence of the two spaces and conversion of parameters from p-q space to I1-J2. This conversion is based on relation between the pressure and first invariant of stress tensor & von-Mises stress and second invariant of deviatoric stress tensor. Finally, the converted parameters are used in simulation and the results are compared against the published experimental data. Using this method, the Extended Drucker Prager material model is applied to compaction simulation. The results are validated against published experimental data. Further, the results from simulation output include relative density, stress, axial and radial die wall pressures (used in stick-slip condition). These parameters help in predicting goodness of compaction upfront and highlight the region prone to cracking and chipping off post compaction.